Materials Integration
Domain C
Applications of the Inverse Design MI to Actual Structural Materials(3D Powder Processing)
AIM
The realization of innovative materials and processes utilizing integrated materials development for 3D powder process of heatresistant alloys with intense development competition and CMCs which are super high temperature heat-resistant materials for next-generation transportation and energy equipment, and this development will strengthen industrial competitiveness in Japan.
C1 Development of Additive Manufacturing Process for Ni-based Alloys
Additive Manufacturing(AM)process for Ni-based alloys is an advanced process that can lead to innovations in parts shape and materials properties, and it is expected to be applied to combustion burners for hydrogen gas turbines. However, the AM process requires a complex and widerange parameter optimization. In this research, we are aiming to improve durability of the combustion burners through demonstrating the actual fabrication of new Nibased alloys being found by MI system for the AM process.
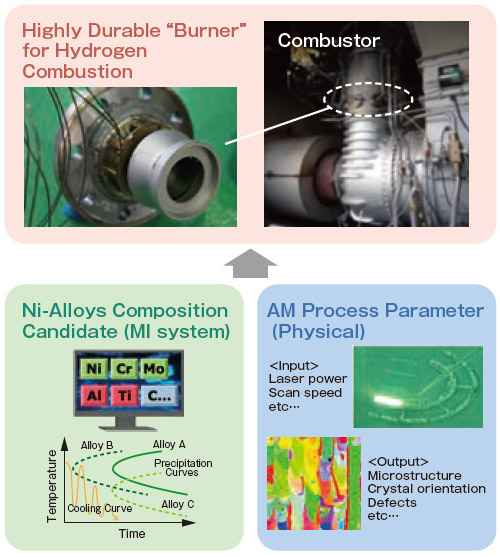
C2 Development of Ni-based Powder Metallurgy Processing for High Performance Aircraft Engine Disk
High-strength Ni-based forged materials by melting process have been used for disk materials for commercial aircraft engines, but Ni- based disk materials made from powder as a raw material are now being applied to high-pressure turbine disks which are in a severe environment, in order to manage an increase in combustion temperature, and this application is expected to expand in the future. We will develop a new process that will be low-cost and enable us to obtain higher mechanical behaviors than conventional western processes, utilizing superior domestic technology.
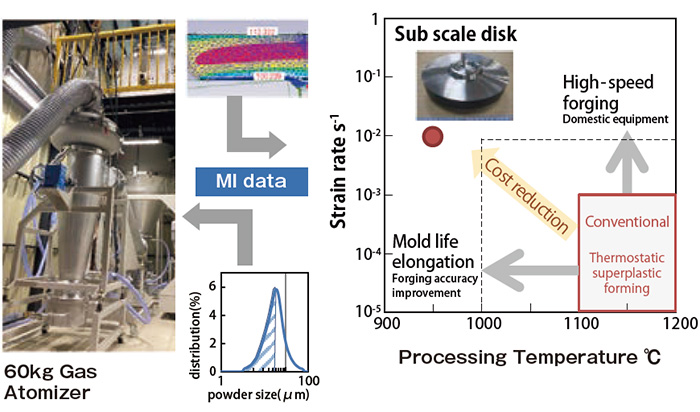
C4 Development of Powder Manufacturing Process and Basic Technologies for High Performance TiAl based Alloy Turbine Blades
In order to develop superior LPT(Low Pressure Turbine) blades made by powder processes of Metal Injection Molding (MIM) and Additive Manufacturing (AM), a sophisticated Materials Integration (MI) system for inverse problems is being built in cooperation with university/industry collaborations. The MI system, consisting of three modules of property prediction (MPM), microstructure design (MDM) and process design (PDM) based on experiments and theoretical calculations, successfully allows us to design a novel alloy to meet the required mechanical properties and geometries for both MIM and AM processes. The outcomes of this project will help enhance industrial strength in Japan.
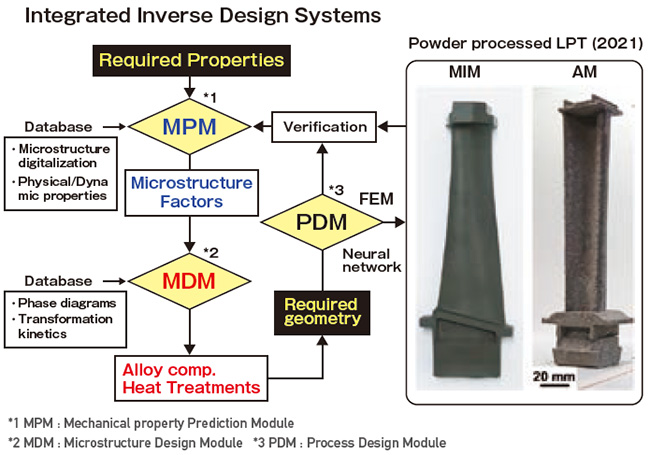
C5 Realistic Simulation of Ceramic Matrix Composites Targeted for High Temperature Components in Jet Engines
A reliability assurance scheme accounting for specificity of Ceramic Matrix Composites(CMCs) is imperative for the deployment of CMCs in high temperature components in jet engines in the near future. We will categorize major issues in reliability assurance into processes, structures and properties, and will overcome these issues by strategic combination of theories, numerical simulations and tests. A virtual test environment will be built to assess the reliability of CMCs hot components of jet engines.
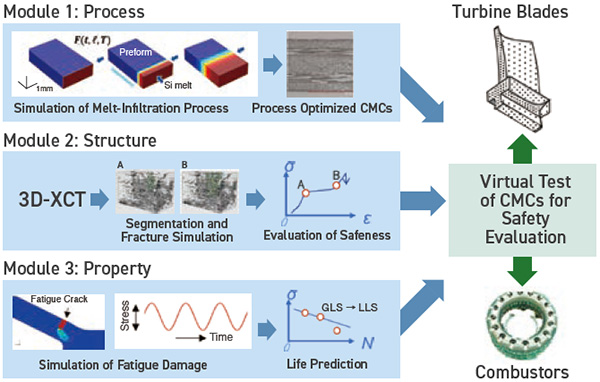
Research and Development
-
- "Materials Integration" for Revolutionary Design System of Structural Materials
- Domain C
Applications of the Inverse Design MI to Actual Structural Materials(3D Powder Processing) - AIM
- C1 Development of Additive Manufacturing Process for Ni-based Alloys
- C2 Development of Ni-based Powder Metallurgy Processing for High Performance Aircraft Engine Disk
- C4 Development of Powder Manufacturing Process and Basic Technologies for High Performance TiAl based Alloy Turbine Blades
- C5 Realistic Simulation of Ceramic Matrix Composites Targeted for High Temperature Components in Jet Engines
- Domain C
- Energy systems of an Internet of Energy(IoE) society
- "Materials Integration" for Revolutionary Design System of Structural Materials