Progress Report
Smart Robot that is Close to One Person for a Lifetime1. Body and control system for smart robots
Progress until FY2022
1. Outline of the project
Current robot hardware is extremely hard and heavy because it emphasizes its accuracy and durability (rigidity). Therefore, for example, it is not possible to essentially clear safety issues for supporting people in daily life, such as customer service, housework, welfare, nursing, and medical care. To solve the above problem, by making the robot hardware, including its constituent parts, skin, joints, etc., essentially “soft”, while having the power to support the whole body of a person, we design and manufacture a robot body that has arms, mobile mechanism and hands that can use various tools, with passive flexibility that does not harm humans even if it collides. Specifically, we develop dry/wet hybrid smart robots with self-repairing and maintenance functions by circulating bodily fluids such as oils, coolants and lubricants that can coexist with humans, in addition to flexible joints, flexible skin, magnetic fluid actuators, and high-precision tactile sensors.
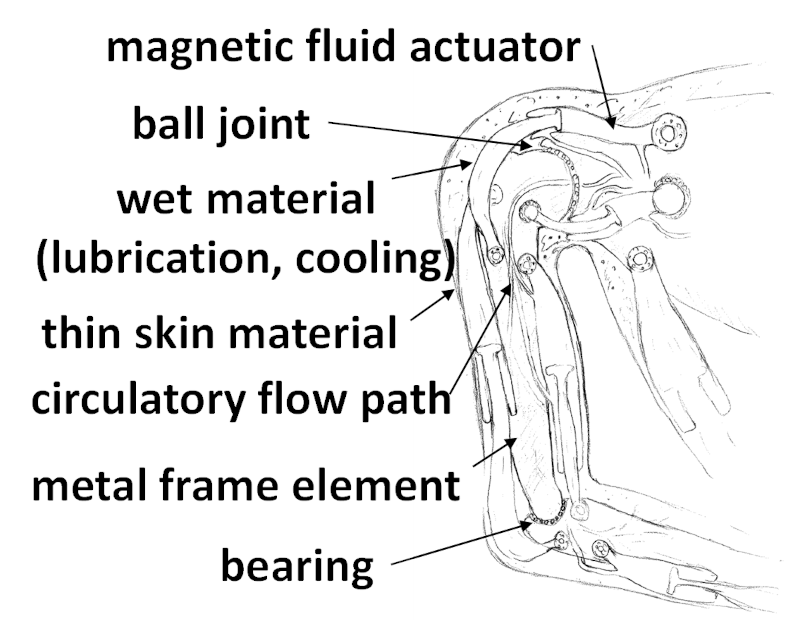
2. Outcome so far
Sub theme 1: Soft robot hardware that can physically support humans with contact
We conducted various experiments on tasks involving physical contact with humans using the world's highest level human-friendly robot (Dry-AIREC). Furthermore, we conducted the following R&D to realize a new dry/wet hybrid smart robot that resembles the human body.
- - Based on skeletal recognition by image processing, we conducted simulated motion experiments of functional training related to expanding the range of motion of joints as nursing care/rehabilitation motions performed by contacting the body (Fig. 2).
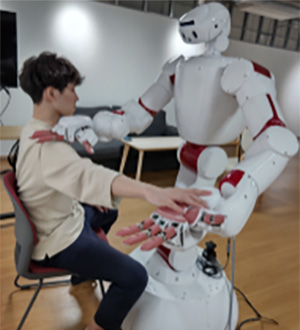
- -We developed the MRF (Magneto-Rheological Fluid) vane motor that serves as the actuator for the hand, and implemented mechanical design for the hand.
- - We established a manufacturing method for self-repairing capsules. Furthermore, we constructed a method for fabricating a channel that allows capsule adsorption, and confirmed that the liquid could be circulated inside the channel using a pump.
- - In order to improve the reliability of the stretchable skin sensor, we confirmed the stability of the output against repeated tension by using coiled copper wire and silicon.


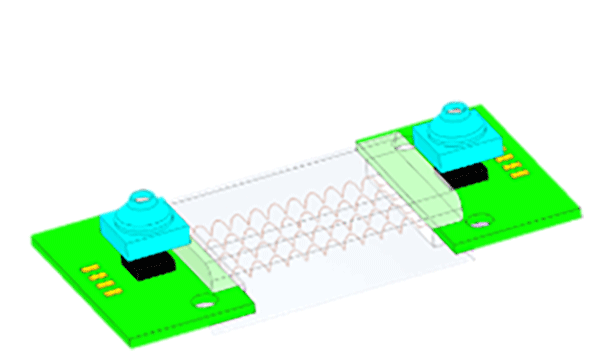
Sub theme 2: Robot middlewa re (OS) for smart robots
By linking OpenRTM and ROS, we realized the operation of Dry-AIREC on the software framework under development. By applying a module that grasps an object by learning using the manipulator's hand coordinates to Dry-AIREC, we confirmed that the same learning model can be used even if the robot is changed.
Sub theme 3: Development of a compiler-coordinated low-power-consumption AI processor that realizes the brains of smart robots
We designed the basic configuration of a low-power AI accelerator processor chip to be installed in a smart robot, and built a design verification and preliminary evaluation environment on FPGA. In addition, we created design information for the next year's chip manufacturing from the basic configuration design.
3. Future plans
We will conduct AI implementation in Dry-AIREC assuming various application scenes involving contact with people, mainly in the nursing care field, and experiments on fluid-driven upper body and hand handling of heavy objects, and fabricate a flow path that allows the adsorption of capsules in the self-repairing function. In addition, we plan to integrate the development of robot hardware, middleware, and AI chips, such as the introduction of compiler-coordinated low-power AI processors into Dry-AIREC.