
セラミックスの高機能化と製造プロセス革新 技術テーマパンフレット2020年11月更新
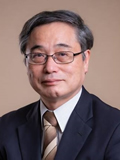
研究開発テーマの設定趣旨
●テーマの概要
セラミックスはさまざまな優れた特性を持ちながら、高価であることや突然の破壊・割れの発生する場合があることが、普及を妨げています。こうしたことから、セラミックスの複雑な製造工程や高温焼成によるエネルギー多消費、製品の内部構造の不均一性に起因するこれらの課題の抜本的な解決と更なる高機能化が求められています。
本技術テーマは、原料粉の合成から後加工までセラミックス製造工程全体を見直して上記欠点を克服する基盤技術を基礎科学に立脚して確立し、製造プロセスのブレークスルーを目指します。これにより、製品の競争力向上や従来品の機能を凌駕するさまざまな特性を実現すると共に、新たな用途の可能性を検討し、優れた特徴を持つセラミックスを社会に広めることを目指します。また、企業での製造に直結することを念頭に、原料粉の製造・成形・焼結・後加工までの製造技術全体を見通し、目視と勘と職人芸に頼る部分を廃し、科学的な観点から生産性の向上と機能向上のための「技術の体系化」に挑戦します。
●公募・選考・研究開発テーマ運営にあたってのPOの方針
セラミック部材は軽量で優れた耐熱性・耐久性・耐食性・機械的特性・電気的特性等の特徴を備えており、多くの分野で使われ、様々な産業を支えています。日本のセラミックス産業が競争力を失うと、日本全体の産業競争力の減退につながりかねません。多方面で使用される重要な素材産業であり、かつ高成長が期待できるセラミックス産業において今後も高い競争力を維持することは、日本のセラミックス産業のみならず、日本の他の産業と日本社会にとって重要な意味を持ちます。
日本では、積層コンデンサーや圧電素子等の電子セラミックス部品を代表とする電磁気・光学用途向けがセラミックス生産額の7割を占めていますが、ASEAN地域の追い上げが激しくなってきています。一方、欧米では環境・エネルギー分野は勿論のこと、機械部品への応用を目指した研究開発が盛んに行われており、日本でもかつて研究に注力していた構造用セラミックスの研究に於いて日本を追い越そうとしています。
セラミックスの欠点は、複雑な製造工程や高温焼成によるエネルギー多消費、製品の内部構造の不均一性に起因する割れ欠けの発生、低い歩留まり、高コスト等です。これらの欠点を解決するための基礎研究を含む革新的プロセス研究は、十分に行われてきたとは言えず、これらの研究を通してコスト競争力の向上や用途拡大につながる基盤技術の形成が求められています。本技術テーマに基づく研究が、セラミックス普及のネックとなっている技術課題をブレークスルーすれば、セラミックスの爆発的普及をもたらす起爆剤となり、性能面だけでなくコスト面においても日本のセラミックス産業の優位性を際立たせることになります。この基盤技術は、セラミックスに共通する課題の解決を目指すものであり、従来からあるセラミックス製各種電子部品、センサー、圧電・蓄電・熱電変換等エネルギー変換素子、水処理用濾過材、等の全てのセラミック部材のコストダウンや高機能化に役立ちます。また、自動車、ロボット、航空宇宙、半導体製造装置等構造用部品材料の軽量化、省エネルギー化、メンテナンスフリー化、更に、新しいセラミックスの応用分野として期待されている次世代エレクトロニクス・パワーエレクトロニクス、エネルギー、環境浄化、医療・ライフサイエンス、等の様々な分野で、日本の技術的優位を確実にして世界市場をリードする武器となり得ます。
本技術テーマは、セラミックス製造プロセス全体で、目視と勘と職人芸に頼る部分を廃し、科学的な観点から、コストダウンと特性向上のための技術の体系化を目指すものです。特に、成形体の密度と均質性は、焼結挙動に大きな影響を及ぼし、部材の性能とコストを決める重要な要因であり、現状の技術レベルを超える飛躍が望まれます。具体的な基盤技術として次のような例がありますが、従来の製造技術にとらわれない新しいプロセス研究も歓迎します。
具体的なテーマとしては、次のような例が挙げられます。
・有機溶媒から水系溶媒による積層膜の作製技術
・ナノクリスタル、ナノシートからの革新的機能を有するセラミックスの製造
・自己組織化、外場印加等による微構造の革新的制御技術
・高機能を有する有機・セラミックス複合材料の革新的創製技術
また、革新的な特性を有する目標製品の製造に適したプロセスに関する研究や革新的プロセスを基に革新素材創製に挑戦するという観点からの課題もあるでしょう。
特に、合成、評価、理論・シミュレーション技術の連携した異分野の研究者が集まった研究チームによる提案を歓迎いたします。
尚、戦略的イノベーション創造プログラム(SIP)革新的設計生産技術及び革新的構造材料プロジェクトで研究開発が進められているセラミックスコーティング、3D造形技術は、本技術テーマでは取り上げません。
本技術テーマの下で生まれた技術を実用化するには、その技術の達成度や適用可能範囲によって、個別企業が引き取って研究を続ける場合、個別企業と大学らとの共同研究に進む場合、あるいは複数の企業と大学らが集まるコンソーシアムで共同研究を行う場合、等が想定され、将来、この共通の土台が核となって、新しい技術の共創が更に進むことが期待されます。
本技術テーマに即した課題群を、大学・公的研究機関等で科学的な見地から研究し、その成果を産業界にフィードバックすれば、各企業は自社製品に適用して、コストダウンや製造工程の革新、従来品を超える特性を実現することになり、これこそが産業界が望む産官学が連携して生み出すブレークスルーとなります。
テーマの評価
追跡評価
プログラムディレクター(PD)
プログラムオフィサー(PO)及びアドバイザー
役 職 | PO・アドバイザー | |
氏 名 | 所属機関・役職 | |
プログラム オフィサー |
目 義雄 | 物質・材料研究機構 特命研究員 |
アドバイザー | 伊吹山 正浩 | デンカ株式会社 新事業開発部 シニアテクニカルアドバイザー |
アドバイザー | 加藤 一実 | 産業技術総合研究所 理事 |
アドバイザー | 久保寺 紀之 |
株式会社村田製作所 執行役員 技術・事業開発本部 マテリアル技術センター長 |
アドバイザー | 後藤 孝 | 東北大学 名誉教授、未来科学技術共同研究センター 客員教授 |
アドバイザー | 篠崎 和夫 | 東京工業大学 名誉教授、特命教授(教育・国際連携本部) |
アドバイザー | 須山 章子 |
東芝エネルギーシステムズ株式会社 エネルギーシステム技術開発センター シニアエキスパート |
アドバイザー | 仲川 彰一 |
京セラ株式会社 研究開発本部 デバイス研究開発統括部長 兼 先進マテリアルデバイス研究所長 |
アドバイザー | 中野 裕美 |
豊橋技術科学大学 教育研究基盤センター 教授 学長特別補佐(ダイバーシティー推進担当) |
アドバイザー | 中村 賢治 |
トヨタ自動車株式会社 モノづくり開発センター モノづくり開発統括部ワンストップサービス室コンシェルジュG 主査 |
課題
課題名 | 課題概要 |
研究責任者 (所属機関) |
評価結果 | 完了報告書 |
セラミックスプロセスチェーン最適化を目指した構造形成過程のリアルタイム3次元OCT観察法による理解とその制御因子の科学的解明 | 光コヒーレンストモグラフィーを用いたセラミックスプロセス中の構造形成過程のリアルタイム3次元観察による理解と、粒子界面設計およびマスターシンタリングカーブを基軸として構造形成過程の制御因子の科学的解明を行い、セラミックスプロセスチェーンの最適化を目指す。得られた成果を活用して、具体的なセラミックスとして透明体、配向体、積層体を実現する。 |
多々見 純一 (横浜国立大学) |
(平成30年度実施)
(令和2年度実施)
|
|
セラミックス粉体の超微粉砕技術の確立と革新的粉体プロセスの開発 | セラミックスの品質向上とコスト低減の基盤である超微粉砕の制御技術は、いまだに確立されていない。そこで、粉砕時の媒体ボールなどの運動状態のシミュレーションによって実験結果を解析し、粉砕限界粒子径、凝集粒子形成を支配する制御因子を体系的に明らかにする。また、この解析ツールを用いて不純物混入を抑制する粉砕方法や高品質のコロイド調製技術を提案し、粉砕技術の新展開として非加熱のナノ粒子合成プロセスを開発する。 |
加納 純也 (東北大学) |
(平成30年度実施)
(令和2年度実施)
|
|
非鉛圧電配向体の焼結しない低温作製法の確立 ~IoTセンサーおよびエネルギーハーベスター応用に向けて~ | サブミリメートル厚さの非鉛圧電配向体を、水熱法を基にしたプロセスにより焼結することなく、KやNa成分などの熱揮発を生じることなく作製する。センサーや発電機の性能指数を結晶配向性と材料組成の制御によって最大化し、高性能圧電材料の利用を通じて環境にやさしい非鉛圧電体を用いたIoTセンサーおよびエネルギーハーベスター応用を目指す。 |
舟窪 浩 (東京工業大学) |
(平成30年度実施)
(令和2年度実施)
|
|
フラッシュ焼結の学理構築と革新的焼結技術への展開 | 強電場を印加することで、大気中無加圧下で低温・短時間焼結を実現する新たな焼結法であるフラッシュ焼結を確立させ、セラミックス焼成プロセスの革新的省エネルギー化を達成するとともに、接合技術の開発を行う。粒界・界面の先端ナノスケール計測と理論計算シミュレーションを連携させて強電場下の素過程を解明し、フラッシュ焼結の基礎学理を構築するとともに、産業展開のためのプロセス設計指針を示すガイドラインを整備する。 |
山本 剛久 (名古屋大学) |
(平成30年度実施)
(令和2年度実施)
|
|
セラミックススラリーの新規分散評価技術を中心としたスラリー特性の完全定量化による湿式成形プロセスの高度化 | スラリー中の粒子分散状態を的確に評価できる簡便・安価な方法及び装置を開発する。粒子間相互作用の直接測定法および新規シミュレーション法との融合により、勘と経験によらない最適スラリー調製を実現する。さらに微粒子の良分散・高濃度スラリー調製を可能にするスラリー高濃縮装置を開発し、セラミックス成形プロセスの高度化に貢献する。 |
森 隆昌 (法政大学) |
(平成30年度実施)
(令和2年度実施)
|
|
ナノブロック高次秩序化による配向性ナノ構造体の開発と表面ドーピングによる高機能化 | 各次元の高比表面積ブロックとして2次元シート、1次元ニードル、0次元粒子を合成し、高次秩序化により配向性ナノ構造体を開発する。ナノブロックの表面ドーピングにより表面電子物性などを変調し、高機能化・高活性化を図る。特に、常温、常圧、水溶媒での自己組織化により、産業基盤部材となる高比表面積・高活性ナノ構造体の開発を行う。ナノ構造制御に加え、低コスト製造、有機材料との複合化、大面積化を図る。 |
増田 佳丈 (産業技術総合研究所) |
(平成30年度実施)
(令和2年度実施)
|
|
単結晶ナノキューブの自己組織化を利用した新成形技術の開発 | 革新的誘電性能を示すチタン酸バリウム単結晶ナノキューブについて、溶媒蒸発時にナノキューブ間に働く毛管力の制御や自己組織化挙動の最適化により、塗布、印刷、シート成形技術などへの適用を検討し、大面積かつ高規則配列の3次元ナノ構造体を形成する。レーザー照射や静電噴霧などの低温成膜技術を検討し、ナノキューブ間の界面制御を可能にする。これにより、飛躍的な電子・電気物性を検証し、次世代デバイスの設計指針を得る。 |
三村 憲一 (産業技術総合研究所) |
(平成30年度実施)
|
|
無焼成セラミックスプロセスの解析とそれに基づく革新的材料の創生 | セラミックス製造におけるエネルギーの半分以上を消費する焼成工程が不要な無焼成セラミックスは、エネルギー的観点からのみでなく、難焼結性セラミックスの固化、ポリマーや金属との複合化など革新的プロセスとなる可能性が高い。ところが、その強度発現メカニズムの解析は十分ではなく、職人芸的要素が高い。そこで、この部分をセラミックス成形前プロセス解析技術とシミュレーションを用いて材料設計可能なレベルに底上げする。 |
藤 正督 (名古屋工業大学) |
(平成30年度実施)
(令和2年度実施)
|
|
磁気科学プロセスによる単結晶性セラミックスの創出 | 回転変調磁場を用いた磁場配向法は室温で三軸結晶配向が可能な非真空の材料作製プロセスとされ、エピタキシー技術にはない技術的優位性をもつ。磁場配向とコロイドプロセスの融合による異方的機能物質の擬似単結晶セラミックスの創出を目的とし、造粒(合成条件・双晶・粒径)、磁場配向条件(磁場、回転条件、粘性)、焼結条件(温度、圧力、雰囲気)の最適化により、90%以上の緻密性と10度以内の配向度を目指す。 |
堀井 滋 (京都先端科学大学) |
(平成30年度実施)
|
|
反応性プラズマを援用したセラミックス材料のダメージフリー形状創成・仕上げ加工技術の開発 | 硬脆難加工材料である機能性エンジニアリングセラミックス材料に対して、反応性プラズマを援用した『プラズマナノ製造プロセス』の適用により、高能率かつダメージフリーに目的形状を得るプロセスを開発する。本プロセスにより、従来の機械加工技術では不可避であった機械的・熱的・化学的な特性を低下させるマイクロクラックなどの加工変質層の形成を回避できるため、金型の作製などに応用すれば寿命の飛躍的な増大が期待できる。 |
山村 和也 (大阪大学) |
(平成30年度実施)
(令和2年度実施)
|
|
レイヤード結晶シェルによる“単一結晶面粒子”の創製とその超精密機能化 | 1つの結晶面しか持たない“単一結晶面粒子”を創製し、革新的なセラミックス機能制御プロセスを開発する。従来の概念では、セラミック粒子には複数の結晶面が存在するが、有機・セラミックスの共創により“単一結晶面粒子”を合成する。結晶面は機能と直結するため、究極の単一機能を有する粒子が得られ、その3次元構造化により超精密機能化を実現するという革新的なプロセスの確立を目指す。 |
永田 夫久江 (産業技術総合研究所) |
(平成30年度実施)
(令和2年度実施)
|
|