Research Results
From medical devices to household items
MPC polymer; harmless to the human body FY2016
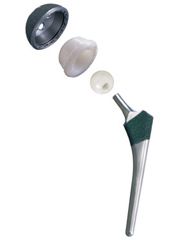
- NOF Corporation / Nobuo Nakabayashi (Emeritus Professor, Tokyo Medical and Dental University) / Kazuhiko Ishihara (Professor, The University of Tokyo)
- Development of Creative Technology Seeds, Contract Development
- "Manufacturing technology of polymer with phospholipid polar group" Developing and implementing company/Representative Researcher (1994-1999)
- Kyocera Medical Corporation (formerly Japan Medical Materials Corporation) /
Kozo Nakamura (President of National Rehabilitation Center for Persons with Disabilities) /
Kazuhiko Ishihara (Professor, The University of Tokyo) - Development of Creative Technology Seeds, Contract Development
- "Long-life Artificial hip joint with high endurance by MPC treatment" Developing and implementing company/Representative Researcher (2006-2011)
MPC polymers are changing medical science
Most people are aware of the word'polymer,'but few are able to answer correctly when asked what a polymer is. In terms of items in daily use, the highly moisture- absorbent polymers used in paper diapers and bed sheets etc. and automotive polymer coatings are probably the best known. Although these both bear the name'polymer,' their uses are completely different;' polymer'is a chemical term referring generally to a molecular organic compound, and many types exist.
One such polymer plays an important role on the front line of medical treatment. This is MPC polymer (a polymer possessing phospholipid polar groups), which was the subject of long years of joint research by Emeritus Professor Nobuo Nakabayashi and Professor Kazuhiko Ishihara.
One major problem with the silicon and polyethylene used to manufacture medical tubes and catheters is that often when introduced into the human body, the body rejects it as foreign matter, causing rejection responses such as blood clotting etc. This problem has been solved by MPC polymer. MPC polymer contains phospholipids, which constitute a major component of biological membranes (cell membranes); thus, simply coating silicon or polyethylene with MPC polymer makes it extremely difficult for proteins or blood cells to adhere.
Artificial hip joint which formed the MPC polymer layer on the polyethylene surface
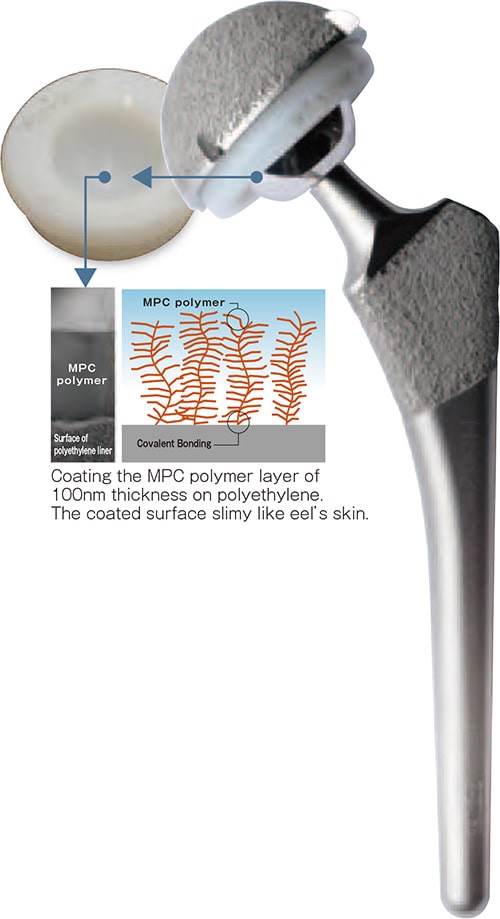
Provided by: Kyocera Medical Corporation
The challenge from producing 1 gram per year
Before the development of MPC polymer, artificial blood vessels were between 10 mm and 20 mm in thickness. However, using MPC polymer, blood vessels can be made as small as 2 mm thick without obstructing blood flow. In this way, MPC polymer has brought a groundbreaking new innovation to the front line of medical treatment. However, synthesizing the polymer was extremely difficult; in 1978, when the compound was initially synthesized, less than 1 gram per year was produced. No matter how miraculous the substance, practical implementation was not possible on this scale, and so realization of the mass production technologies soon became an urgent issue. Under the JST's Contract Development, the NOF Corporation which JST invested 800 million yen as the development expenditure proceeded the mass production development. Finally the development was highly successful, as a result, it has become possible to produce pure high-grade MPC polymer in large quantities these days.
The challenge of long-life artificial hip joints
With mass production now enabled, MPC polymer is currently meeting the new challenge of another medical issue: the longevity of artificial hip joints. We may not often hear about them, but there are actually 40,000 or more artificial hip joint replacement surgeries conducted in Japan alone each year. Although the causes of joint function disorder are diverse, in all cases this surgery involves replacing hip joints that have lost their normal function with artificial hip joints. However, there is one major problem with this surgery. With the passing of time, the components wear down, due to constantly grinding against each other, which causes the artificial joint to slacken and become loose. According to overseas data, around 10-20% of those receiving artificial hip replacements in the 1970s have subsequently undergone another hip replacement surgery.
This fact drove the medical community to seek development of a material that does not wear down, in order to ensure long-term use. Eventually, it was Japan Medical Materials Corporation (JMMC) that resolved this difficult issue, by utilizing the JST's Contract Development. By coating polyethylene components with MPC polymer, the antiwear property of articular surfaces was improved, thus JMMC succeeded in developing artificial hip joints that are expected to have a longer service life.
Friction experiments using hip joint simulator
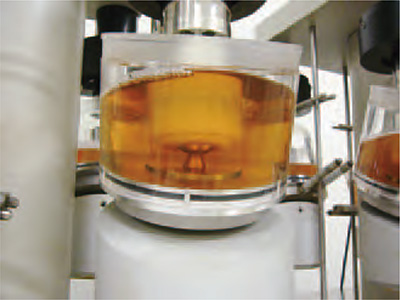
Further expanding the possibilities of MPC polymers
"Using biocompatible materials, I want to create a bio- interface to build a bridge between the human body and artificial materials,"says Professor Ishihara. A bio- interface refers to an interface that does not trigger a rejection response between a living body and artificial materials. MPC polymer, which is currently already in use for artificial hearts etc., certainly promises to be an effective material for creating bio-interfaces in future.
In order to further promote the many uses of MPC polymer, Professor Ishihara also provides samples of MPC polymer to interested researchers around the world. He hopes that by so doing, the potential uses for MPC polymer, originally developed for medical applications, will be greatly expanded. These efforts have ensured that MPC polymer is now utilized in a diverse range of fields beyond the medical profession, including practical implementation in contact lens care products, cosmetics materials, textile processing agents, and much more.
With further great leaps forward expected in the fields of medicine and engineering, MPC polymer is certain to become an essential part of our daily lives in future.
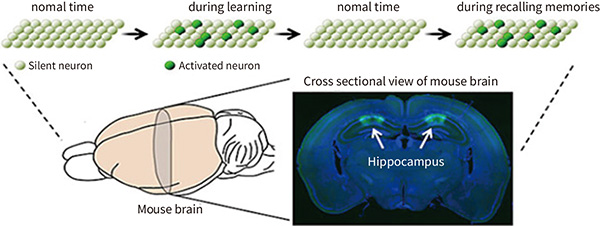
MPC polymers are used widely across a range of fields