Research Results
A once-in-a-century technological innovation
New developments in ammonia synthesis FY2018
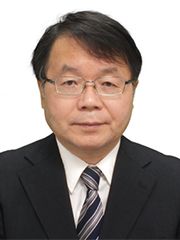
- Hideo Hosono (Professor, Laboratory for Materials & Structures , Institute of Innovative Research, Director, Materials Research Center for Element Strategy, Tokyo Institute of Technology)
- ERATO
- "Hosono Transparent ElectroActive Materials Project" Research Director (1999-2004)
- SORST
- "Exploring and Developing Applications for Active Functions Utilizing Nanostructure Embedded in Transparent Oxides" Research Representative (2004-2010)
- ACCEL
- "Materials Science and Application of Electrides" Research Director (2013-2018)
Ammonia synthesis requires large-scale production facilities
Ammonia is widely used as a raw material in nitrogen-based fertilizers, foodstuffs, medicines, and so on, and annual global production exceeds 170 million tons. The primary use for ammonia is fertilizer and population growth and the resulting increases in food production mean that demand for ammonia is expected to see continued growth. On the other hand, the fact that ammonia molecules can be used to produce hydrogen by breaking them down, and the fact that it can be easily transported in liquid form, means that ammonia is also garnering a great deal of attention as a source of hydrogen for fuel cells and so on.
The current ammonia synthesis method is the Haber-Bosch process, which involves reacting atmospheric nitrogen and hydrogen produced from methane using an Iron-based catalyst. More than a century after its introduction as an industrial production process in ermany in 1913, the Haber-Bosch process is still the primary method used to industrial synthesize ammonia. Reacting nitrogen gas that is chemically very stable, requires high temperatures (400 to 500°C) and pressures (100 to 300 atm), and to make ammonia production commercially viable therefore requires enormous production facilities.
While rofessor Hideo Hosono and his team have primarily focused on R&D work on new high-performance materials such as superconductors and transparent transistors, one offshoot of this involved the development of materials with catalytic functions. The team realized that if it were possible to synthesize ammonia using a high-performance catalyst able to generate reactions at lower temperatures and pressures it would likely be possible to produce ammonia at smaller facilities using production methods suited to the flexible use of the resulting ammonia. It was with this in mind that they took on the challenge of developing such a catalyst.
Technologies essential for daily life
Professor Hosono says "I don't consider substances that aren't used in the real world to be materials at all. I want to create things that people actually need. Synthesizing ammonia to use as fertilizer to produce foodstuffs felt like a perfect task for me to tackle". He knew that the key to finding a solution would be finding a catalyst that would react with nitrogen. Electrides* such as C12A7 electride (C12A7:e-) developed by professor Hosono and his team in 2003 as a result of their ERATO program research, have work functions that are as low as alkali metals, that is, they are unique in that they easily emit electrons while remaining stable. The team reported in 2012 that by depositing nanometer-size ruthenium particles (which function as catalysts) to the surface of C12A7:e-. It is possible to efficiently synthesize ammonia at lower temperatures (340 to 400°C) and lower pressures (l atm) than is possible with conventional methods.
In 2014 and 2015 they also revealed that an entirely unique reaction mechanism works for Ru-loaded C12A7:e- catalyst. The team discovered that chemical reactions required less than half as much activation energy as other catalysts and that the process of severing nitrogen molecules proceeds smoothly. They also discovered that hydrogen dissociated on the surface of Ru nanoparticles is preferentially absorbed by the C12A7:e- during reactions and hydrogen poisoning-which reduces catalytic activity through the absorption to the active sites on Ru at elevated hydrogen pressure-does not occur. This delineated a path toward a more efficient ammonia synthesis method with less restrictive conditions.
The ammonia synthesis mechanisms over conventional
catalyst (left) and Ru/ C12A7:e- (right)
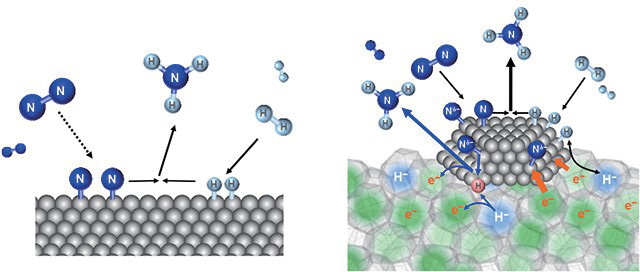
On Ru/ C12A7:e-, the electrons in the cages are transferred to ruthenium (Ru) and when this moves to nitrogen molecules adsorbed on the Ru particles, the severing of nitrogen triple bonds (N≡N) is cleaved easier. Hydrogen that has been severed on ruthenium is brought inside the cage as H- ions through reaction with electron in the cage and emitted as atomic hydrogen (leaving an electron in the cage) which reacts with the nitrogen atoms on the Ru particles thereby producing ammonia.
* "Electride" is a general term used to refer to ionic compounds with electrons that operate as anions. 12CaO•7Al O (C12A7) takes on a structure featuring interlinked 0.5nm cages with oxygen ions inside them. hen, in 2003, rofessor Hosono and his team replaced these oxygen ions with electrons, they discovered that the compound became stable even when exposed to air, that it changes into a form that allows electricity to flow well from insulators, and that it gains the ability to supply electrons externally, and they named it C12A7 electride( C12A7:e-).
A once-in-a-century technological innovation
Although Professor Hosono and his team knew that catalysts that utilize C12A7:e- have considerable ammonia synthesis capabilities, one issue to be addressed on the way to the method' s commercialization was how to further enhance the catalytic performance per unit weight. To achieve this they sought out materials better equipped with more favorable nature and dynamic structure from which C12A7 electride s high level of catalytic activity originates, and they shifted their attention to a material called calcium amide (Ca(NH2)2). Calcium amide itself is thermally unstable and easily decompose, but it was discovered that attaching ruthenium to it makes it stable for long periods of time and allows it to function stably for long periods of time as an ammonia synthesizing catalyst. That' s more, they succeeded in synthesizing ammonia at relatively low temperatures (300 °C or lower) with an efficiency more than l0 times higher that of conventional catalysts. With the addition of barium, the team also discovered that catalytic functions were further improved with the ability to sustain catalytic activity without attrition for more than 700 hours (approximately one month).
The ammonia synthesis method of rofessor Hosono and his team, which could be said to be the realization of something that has been dreamed of for a century, is now close to being commercialized on an industrial scale.
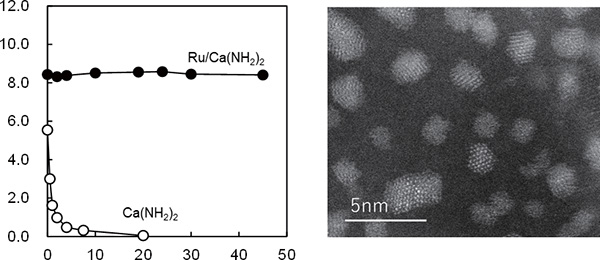
(Left) Time course of HH3 synthesis over Ca(NH2)2(○) and over ruthenium loaded Ca(NH2)2, ●)
(Right) Electron microscope image of Ru/Ca(NH)
The performance of Ru catalysts developed so far
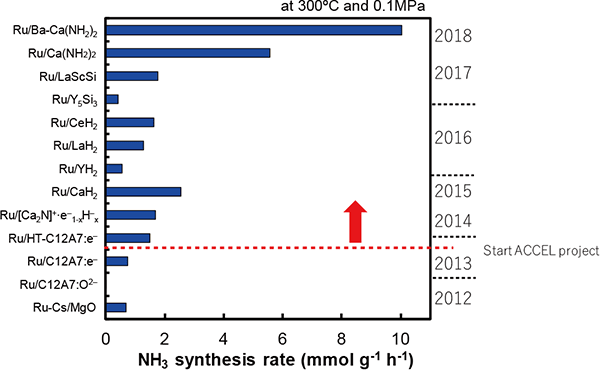
Performance has been enhanced by 10 times at ordinary atmospheric pressure and by 30 times at 0.9 MPa compared with that of catalysts prior to the launch of the ACCEL roject.
A project aimed at perfecting the synthesis process has now been launched
The new ammonia catalysts invented by rofessor Hosono and his team will facilitate production cost reductions through reduced energy use and production facility downsizing. They will also enable companies that utilize ammonia as a raw material for chemical products to install small-scale ammonia production facilities in their own factories.
In April 2017, a sovereign wealth fund niversal Materials Incubator Co., Ltd. and a food producer Ajinomoto Co., Inc. established a new company with the aim of commercializing the new ammonia production technologies developed by rofessor Hosono and his team. Ajinomoto Co., Inc. uses a large amount of ammonia in the production of their mainstay product "umami seasoning". The company currently procures their ammonia from external sources and this, in addition to the need for dedicated vehicles to transporting ammonia and storage tanks etc. involves substantial costs. If they were able to produce ammonia onsite they could be expected to be able to significantly reduce their production costs and production flexibility. The newly established company is aiming to commercialize small-scale ammonia production processes by 2021.
This is the world's first initiative aimed at facilitating "onsite ammonia synthesis" to produce ammonia where and when needed. In addition to its use in food production, this process will presumably also be employed in the constantly increasing range of other areas in which ammonia is used such as the fertilizer and energy fields. The new company will first move ahead with research and development into commercialization and intends to introduce the process into a wide variety of different industries in the future.