Research Results
Successfully passed the global standard with half precious metal catalyst!
Emission gas purification system derived from paper making technology FY2016

- F.C.C. Co., Ltd. / Takuya Kitaoka (Professor of Graduate School of Faculty of Agriculture, Kyushu University)
- Development of Creative Technology Seeds Contract Development
"Emission gas purification system using wet paper making method" Development and implementing company / Representative Researcher (2006-2010)
Paper making technology changes the future of emission gas purification
To control emission of greenhouse gas that contributes to global warming, emission control has been implemented on vehicles and motor cycles all over the world.
A conventional emission gas purification system is made of a honeycomb-structured ceramics or stainless steel coated with ternary catalyst using platinum, rhodium and palladium, that makes nitrogen oxide, carbon hydride and carbon monoxide contained in emission gas harmless. However, with many concerns, such as resource protection and stable supply, a new purification system is needed. Amid this, the Emission gas purification system using wet paper making method was developed on the Development of Creative Technology Seeds, Contract Development by Professor Takuya Kitaoka and F.C.C. Co., Ltd. This unique method is based on Japanese traditional technique called "kamisuki (paper making)".
There is an urgent need to develop a purification system with less quantity of precious metal
Production of vehicles and motorcycles has been expanding all over the world. Strengthening of emission gas control will continue in the future. A conventional purification system responded to strengthening of the control only by increasing the quantity of precious mental used as a catalyst. However, this method has reached its limit. It is impossible to continue to use limited resources such as platinum and rhodium at the current rate. It was an urgent issue to develop an effective emission gas purification system using less precious metal.
Production of an innovative new catalyst by wet paper making method
Professor Takuya Kitaoka had been exploring the possibilities of a new catalyst. He thought it possible to provide effective emission gas purification if he made a catalyst structure with many pores like paper. Then, he found a crutch maker, F.C.C. This company used papermaking technique to manufacture a friction material as the major component of a crutch. Can this technique be applied? Then, their innovative joint research started.
After many twists and turns, they reached a method called the "wet paper making method". In this method, a material containing powder of ceramics and pulp is sheeted like making thin hand-made Japanese paper. By rewinding it, it is shaped into a honeycomb-shaped structure. By highly heating it and adding palladium and rhodium as catalysts, they accomplished a new emission gas purification system.
What did the quantity of precious metal in it become? Surprisingly, there was no need to use platinum. Then, the system successfully passed the current global standard, EURO3 as a European emission standard for motorcycles (carbon monoxide: 2.0 g/km or lower, carbon hydride: 0.3 g/km or lower, nitrogen oxide: 0.15 g/km or lower) with around half the conventional quantity of precious metal. This improved the efficiency while achieving significant cost reduction. It has higher heat resistance, which a conventional system did not have, and a conspicuous characteristic that its purification performance does not decrease even at 1000 degrees C.
F.C.C. had already commercialized paper catalyst. They produced an innovative result using a conventional paper making technique.
Production process of new system
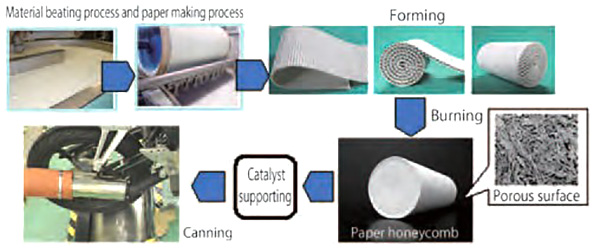
(1) Material beating process and paper-making process: Paper is made from mainly ceramics powder and pulp and paper sheet is produced.
(2) Forming: Rewinding it into a corrugated shape after forming produces a honeycomb-shaped structure.
(3) Burning: It is burned at higher temperature (organic components are burnt/pores are formed).
(4) Catalyst supporting: Palladium-supported and rhodium-supported magnetoplumbite are coated and they are fired and fixed at lower temperature.
(5) Canning: A ceramics mat is used as a supporting material on the stainless steel pipe to press the honeycomb structure.
Emission gas purification system using wet paper making method
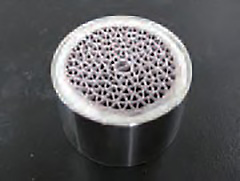
Development to hydrogen production catalysts and photocatalysts is expected
This system is light and easy crushable into small pieces for recycling of precious metal because the honeycomb structure is made of porous ceramics. Passing standards of strength enough to mount on a vehicle and purification performance, as the system is cost effective, it is greatly expected that it is used on general machines and motorcycles. In addition, development of the structure specific to paper by the new technique to hydrogen production catalysts and photocatalysts is expected. Anyway, the result of this R&D will continue to contribute to environmental problems that will get more acute in the future.
* Substance that increases the speed of the chemical reaction but does not change itself or its action. It has specificity to create only the desired products.