Research Results
Heat-release design crucial to Smartphones
High-quality graphite sheet FY2016
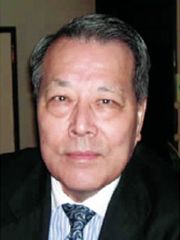
- Susumu Yoshimura (Visiting Professor, Nagasaki Institute of Applied Science)
- Risk-Taking Fund for Technology Development
- "Development of high-quality graphite manufacturing process" Team Leader (1988-1992)
- ERATO
- "Organic Electronic Materials Group in OGATA Fine Polymer Project" Group Leader (1981-1986) "YOSHIMURA π-Electron Materials Project" Reserch Director (1991-1996)
In search for innovative graphite manufacturing process
Graphite, a crystalline form of carbon, is an element mineral composed of carbon alone. Because it effectively diffract or transmit radiations such as x-rays, it is used as optical elements of radiation. Usually, natural graphite occurs in a powder form, and its crystalline form is rarely obtained. Instead, artificial graphite has been used for industrial applications. The material, however, requires complex manufacturing processes, a considerable period of process time and is extremely expensive. To develop a process for high-quality graphite in a less expensive way, Matsushita Electronic Components Corporation, one of the subsidiaries of Matsushita Electric Industrial, carried out the development project. Professor Susumu Yoshimura, then a researcher with Matsushita Research Institute Tokyo, headed the project team.
Prof. Yoshimura's team developed the technology for crystallizing carbon at 3000°C.
The key technology that enabled the breakthrough was a heat-treating process on polymeric materials containing carbon. The process was developed by the Organic Electronic Materials Group led by Prof. Yoshimura as a part of ERATO OGATA Fine Polymer Project. As polymeric materials are heated in an inactive gas atmosphere, hydrogen, oxygen and nitrogen atoms are successively released at 500°C, 1000°C, and 2000°C, respectively, eventually leaving carbon alone. The carbonaceous material is crystallized into highquality graphite through subsequent heat-treatment at over 3000°C temperatures. The development team investigated various polymer materials at different heattreatment temperatures and eventually discovered that specific polymer materials (such as polyimides) can be crystallized into graphite over 3000°C (Figure 1). Since it can be manufactured at low cost and in a short process time, the crystalline material was put into use in an industrial basis as optical elements, such as neutron and x-ray monochromators.
Figure 1
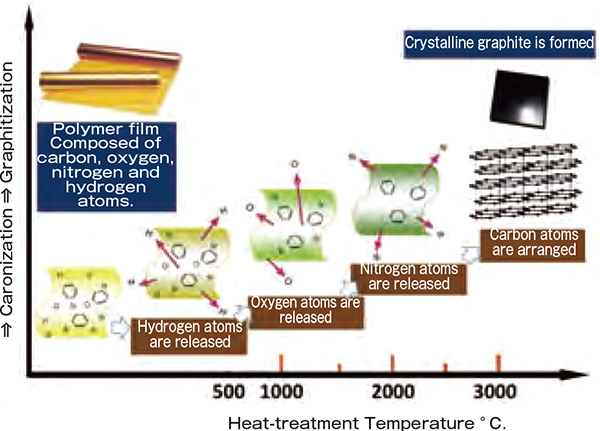
As polymeric materials are heated, hydrogen, oxygen and nitrogen atoms are successively released, eventually leaving carbon alone. The carbon is then heated at 3000°C to form crystalline graphite.
The graphite sheet is able to efficiently release the heat.
At the time when the novel manufacturing technology of graphite came into existence, the mobile terminals including mobile phones had been rapidly gaining popularity and the devices had been underway toward miniaturization and sophistication. Central processing units (CPUs), which drive those devices, tend to lose their performance due to the heat caused by their operation. The challenge, therefore, was how to efficiently release the heat. Graphite sheets provided a definitive solution to the issue (Figure 2).
Figure 2
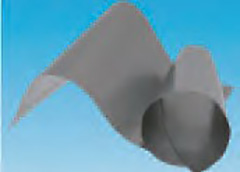
"Panasonic Graphite Sheet (PGS) 10µm-thick product," launched for Smartphones in September 2012.
Graphite has a layered crystal structure. Its thermal conductivity is very high in the horizontal direction (when heat is transferred over a laminar plane), while it is approximately 200-fold lower in the perpendicular direction (when heat is transferred upward/downward) (Figure 3). The graphite sheet came to be extensively used as materials that release heat once applied to devices . It also has great flexibility and the characteristics allowed it to be used to cover heat sources with differences in level (Figure 4). In addition, it has lower specific gravity and higher strength than metal materials. The advantage also greatly contributed to miniaturization and higher durability. As carbon crystals, graphite has extremely lower environmental burden, which was another characteristics preferred by manufacturers. Now, the material has opened up a 100 billion-yen market globally, which is incredible as for the passive component.
Figure 3
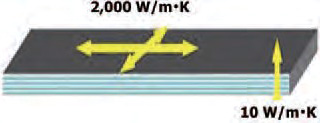
Heat conductivity profile of graphite sheet: It has low heat conductivity in the thickness direction, while it exhibits very high heat conductivity in the surface direction.
Figure 4
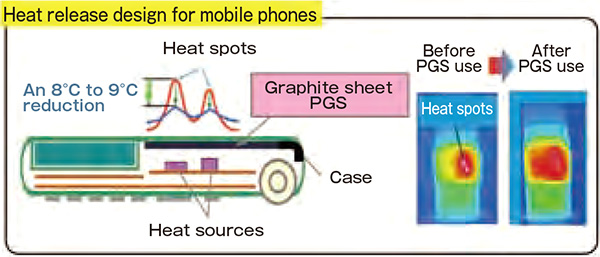
Highly heat-conductive graphite sheet reduces heat spots
New carbon materials with innovative functions
Later, Prof. Yoshimura led the ERATO YOSHIMURA π -Electron Materials project as a reserch director in parallel with his continued efforts to develop new business frontiers for the high heat-conductivity graphite. The"π-electron"mentioned in the project title has an important role on characterizing properties and functions in organic materials. Prof. Yoshimura continued to work for new carbon-based materials and brought a lot of achievements, including low-temperature synthesis of graphite thin-film and carbon nanotube, synthesis of new intercalation compounds that contains alkali metals in graphite and their new quantum effects, development of carbon thin-film-based solar cells, development of polymerization-induced epitaxy process using graphite surfaces and luminescent phenomenon occurring in silica glass containing carbon intermediates. Notably, the technology for synthesizing graphite thin-film and carbon nanotube at low temperature enabled synthesis at 600°C to 1000°C using chemical vapor deposition (CVD) method. The technology opened up a way to synthesizing graphite in conventional semiconductor manufacturing processes.
His scientific achievements on the conditions and control methods applied to CVD-based low-temperature synthesis of carbon nanotube found their successors in an international collaborative work, ICORP Nanotubulite Project, led by Prof. Sumio Iijima, Meijyo University. The project served as seed bed for a new material, "carbon nanohorn." Works have been underway to use the material as an electrode material of fuel cells. The technology will reportedly be coming out soon in practical use. Prof. Yoshimura's achievements in ERATO are bearing fruit across different disciplines.