Research Results
Impact and listen with laser technology
Remotely inspecting the inside of concrete at high speed FY2017

- Katsumi Midorikawa (Director, RIKEN Center for Advanced Photonics)
- SIP
- Infrastructure Maintenance, Renewal, and Management Technology
Research and Development of High-Performance Nondestructive Deterioration Diagnostic Technology for Infrastructure by Using Lasers Principal investigator (2014-)
How to maintain concrete infrastructures
In our country, there are a lot of concrete infrastructures using such as tunnels and bridges. Since many of them were built during the period of high economic growth, there is growing concern about their aging degradation.
In order to maintain and use these infrastructures for a longer period of time, it is necessary to develop appropriate technology for their maintenance and management. Such technology has to be designed in such a way that can reduce maintenance and renewal costs, in addition to alleviating a serious shortage of human resources engaged in maintenance and renewal work. At present, there is a great need for the development of technology that enables precautionary maintenance to find and repair damage to be conducted during an early stage. The Council for Science, Technology and Innovation of the Cabinet Office is functioning as a command center for the promotion of the "Cross-Ministerial Strategic Innovation Promotion Program (SIP)," and one of the challenges addressed by Japan's leading researchers in this program is the difficult task of developing "Infrastructure Maintenance, Renewal, and Management Technology." This challenge involves five research and development items. One of the items is the research and development of the "technologies for inspection, monitoring and diagnosis." Director Katsumi Midorikawa of RIKEN, who is serving as the principal investigator of the research and development issue "Research and Development of High-Performance Nondestructive Deterioration Diagnostic Technology for Infrastructure by Using Laser" in the this item, his fellow researchers and their collaborative research groups (National Institutes for Quantum and Radiological Science and Technology, Japan Atomic Energy Agency and Institute for Laser Technology) are trying to establish a new inspection technology that is completely different from traditional methods. They have been attempting to establish a technology that uses laser to inspect the soundness of tunnel lining concrete at high speed.
Impact with lasers and recognize the difference in sounds with lasers
With regard to a tunnel, the presence of defects such as "cracks" or "float" lining concrete can lead to a serious situation like a collapse. Therefore, it is necessary to detect defects r eliably by conducting periodic inspection as well as to remove and repair them. However, road tunnels and railroad tunnels are present everywhere, and the number of tunnels is great.
Currently, for such an inspection, the method called hammering test is commonly conducted. In this test, a skilled inspector hits concrete with a hammer and diagnoses its soundness by the difference in sounds generated from the inspected concrete. However, this hammering test requires time-consuming work for inspection, so it takes a lot of time to inspect a great number of tunnels. In addition, since it is a contact-type inspection that poses a danger to inspectors, the development of high-speed inspection technology that can be conducted in a non-contact manner has been sought after for a long time.
With that, a new method called the "laser defect detection method" was invented. This method makes it possible to detect defects inside concrete in a remote and non-contact manner, and it is characterized by the use of two types of laser technologies called the "impact laser system" and the "laser measurement system."
The "impact laser system" like a hammer hitting concrete, can produce a vibration on the surface of concrete by irradiating intense laser pulses to the inside wall of a tunnel. The "laser measurement system," like an inspector who diagnoses the soundness of concrete by laser impact, examines the reflection state of lasers to detect if peculiar vibrational components are mixed in the concrete.
The principle of this method has been demonstrated by a joint research team from West Japan Railway Company, the Railway Technical Research Institute and Institute for Laser Technology. In actuality, however, the measuring speed was limited to around twice a second. Therefore, further improvement in inspection speed was desired, and so the joint research group led by Director Midorikawa worked on the improvement of inspection speed.
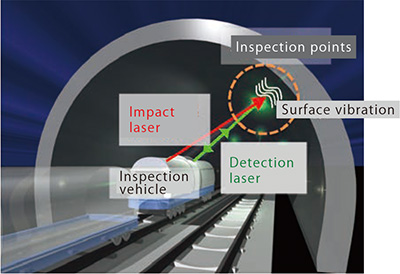
Defect detection method using lasers (image)
Technology that detects internal defects 50 times faster
Generating laser pulses with a high frequency of dozens of times per second is needed to speed up tunnel concrete inspection. With the conventional technology, the quality of lasers deteriorates due to the influence associated with high-speed operation, as a result of which it becomes impossible to impact an inspection object several meters away with lasers. With that, the joint research group led by Director Midorikawa developed an "optical amplifier" that incorporated a dedicated water-cooling system and related devices. As a result, it became possible to produce an impact laser capable of operating under a speed of up to 50 times (50 Hz) per second.
It is necessary to lead lasers into an inspection region precisely and promptly for scanning in order to inspect a tunnel concrete at high speed. Director Midorikawa and his fellow researchers developed a system that can scan both an impact laser beam and a laser beam from the laser detection system at high speed with accuracy by using a galvanometer mirror, a special mirror that can precisely control the movement of lasers at high speed by adjusting electric current.
In addition to these two developments, the speed of vibration measurement and defect determination were increased by improving calculation procedure. Combining these technologies led to the creation of a "high-speed sweeping laser measurement system" that can carry out vibration measurement, defect determination and result display on a real-time basis. Additionally, the joint research group led by Director Midorikawa succeeded for the first time in the world in detecting defects inside concrete, such as cracks, with a laser at a speed of 25 times (25 Hz) per second, which is equivalent to 50 times faster than that of the conventional method.
High-speed sweeping laser defect detection equipment (schematic view)
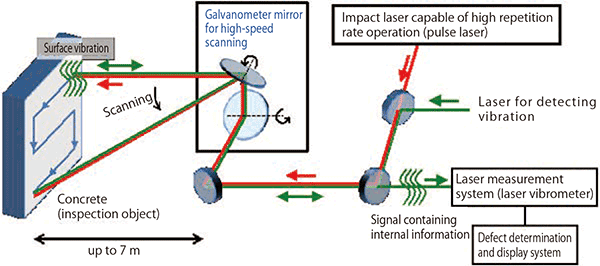
Optical amplifier for impact laser that can operate at high repetition rate (photograph of its appearance)
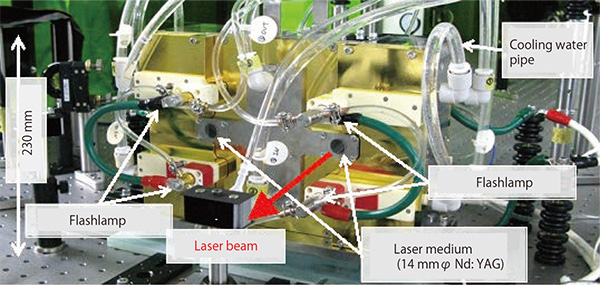
High-speed sweeping laser measurement system (photograph of its appearance)

【Diagnostic result of the soundness of a concrete specimen】
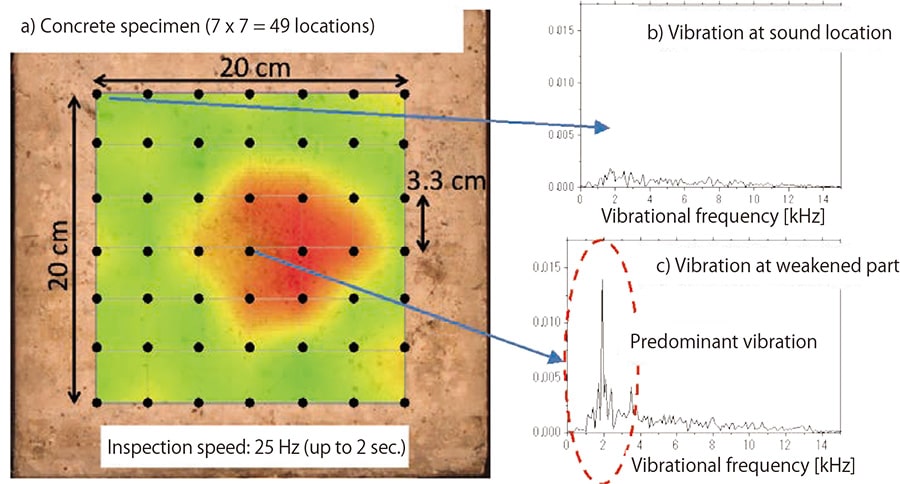
Soundness of concrete specimens that were embedded with simulated defects was diagnosed by using the high-speed sweeping laser defect detection equipment. Black dots represent the location where inspection was performed, and when a defect was present inside the concrete, a specific vibration frequency (predominant vibration) was clearly observed.
Conducting thorough verification and confirmation of accuracy for the speeding-up of inspection
In reality, inside the concrete of a tunnel, there are various types of defects, which vary in depth, shape and size. Continuing into the future, Director Midorikawa and his fellow researchers will conduct thorough verification and confirmation of accuracy, in addition to associating the vast database of sounds related to various defects that were accumulated by using the conventional hammering method with vibration data obtained by using this laser defect detection method, with the aim of establishing a remote and non-contact inspection technology that is compatible with the hammering method.
Since the laser defect detection method developed in this project realizes the automatization of inspection, it is believed that this method will contribute to the optimization and cost reduction of inspection. Moreover, their continuous efforts are expected to lead to the development of a further improved technology that enables various buildings as well as tunnels to be inspected remotely and safely at high speed in a non-contact manner in the future.