Research Results
Versatile and economic polymerization method
Practical application of innovative, advanced color materials FY2017
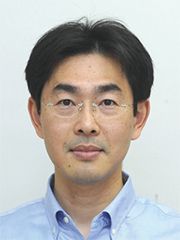
- Dainichiseika Color & Chemicals Mfg. Co., Ltd. Atsushi Goto (Associate professor at Nanyang Technological University, Singapore)
- A-STEP Seeds development type
- "Development of high performance color materials with advanced functions based on living radical polymerization with organic catalyst" (2011–2015)
Features of living radical polymerization
Polymerization refers to the process of connecting low molecular weight compounds (monomers) in chemical reactions to produce thread-like high molecular weight compounds (polymers). Industries often use a method called radical polymerization. However, the length of produced polymers (molecular weights*) is not uniform and the structures of polymers cannot be controlled. Living radical polymerization is a method to overcome this disadvantage. This method can offer polymers with nearly uniform molecular weights and controlled structures (structurally controlled polymers). Such structurally controlled polymers can provide advanced polymer materials which can enrich our daily lives. Living radical polymerization is thus expected to serve as a powerful method for manufacturing high-value polymer products in a wide variety of industrial applications.
Production of various functional polymers at low cost
Industry thus starts to use living radical polymerization. However, high cost is a significant problem among other problems. One of the effective approaches that overcome this challenge is organocatalyzed living radical polymerization that Associate Professor Atsus hi G oto (Kyoto Unive rsit y at that time) invented. Figure 1 shows the concept of this method. This method can significantly cut down the production cost of such structurally controlled polymers because it uses only inexpensive organic compounds as controlling agents (catalysts and initiators). This method is applicable to various functional monomers that can afford various functions such as hydrophilicity and hydrophobicity onto the polymers. This method thus allows tailor-made design of polymers and has great capability and versatility to industrial applications. An example of the useful applications is block copolymer dispersants that are obtainable with this method. Such block copolymer dispersants can finely disperse small particles such as pigments in liquids and resins. Pigments are usually easy to aggregate and conventionally very difficult to disperse effectively.
Figure 1 Living radical polymerization with organic catalysts
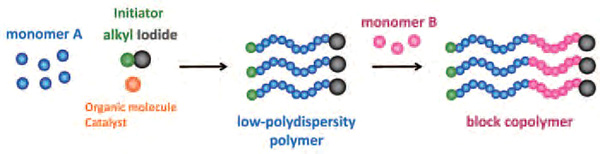
Realization of practical application of innovative inventions with the cooperation of the industry, academia, and government
The journey to our successful commercial application of this polymerization started at a new technology briefing session of nano-materials of JST in 2008. Prof. Goto proposed this method that he had just invented to Dainichiseika Color & Chemicals Mfg. Co., Ltd. and a joint project among the industry, academia, and government began. Dainichiseika Color & Chemicals Mfg. Co., Ltd. positioned this polymerization method as a core technology for developing color materials and targeted color materials superior in the global market.
They aimed to develop new advance color materials and also extend their markets to information technology (IT), environment, and energy, for example. They received a research funding of A-STEP from JST for seeking commercial applications of this polymerization to color and its related materials. In the A-STEP project, they improved the polymerization performance, installed a pilot plant in an industrial scale, developed a variety of new color and color-related materials, and eventually succeeded in commercial applications.
Successful production of high-performance dispersant (color material)
Dainichiseika Color & Chemicals Mfg. Co., Ltd. explored methods to uniformly disperse pigments in water and oil. Figure 2 shows the structures of pigment dispersants. A polymer dispersant consists of two different units. One unit can be adsorbed onto pigments (red dots in the figure) and the other unit can be dissolved in dispersive media such as water and oil (blue dots).
Conventional radical polymerization can provide only random copolymer dispersants (Figure 2, left) in which the mentioned two units (with different roles) are randomly distributed. In addition, the molecular weight is not uniform. On the other hand, our living radical polymerization method can provide block copolymer dispersants (Figure 2, right), in which the mentioned two units are separately distributed in two distinct segments. Random copolymer dispersants can at tach onto pigments in a "dot-like" manner, because the pigment- attaching units (red dots) are randomly distributed in a chain. On the other hand, block copolymer dispersants can attach onto pigments in a "line-like" manner, because the pigment-attaching units form a segment. Therefore, block copolymer dispersants have strong adhesion to pigments. A similar concept is valid in the affinity to dispersive medium. Because of these two reasons, the pigment dispersants synthesized with this technology enable more stable dispersion of pigment particles in various environments and conditions. Along with these researches on product design, the company also installed a pilot plant suitable for this polymerization method (Figure 3). Through these researches and tests, they succeeded in the commercial production of dispersion materials in which nano-particles are finely dispersed in stable forms. Dainichiseika Color & Chemicals Mfg. Co., Ltd. is currently extending their commercial application to various color materials and other new materials.
* The molecular weight is not uniform in synthetic polymer. Synthetic polymers usually have broad distribution of molecular weight.
Figure 2
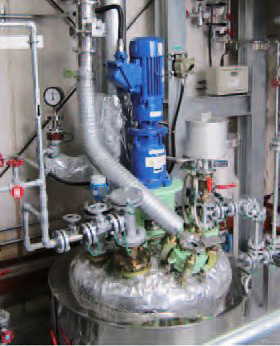
An image of dispersions of dispersant with random copolymer <left> and dispersant with block copolymer <right>
Figure 3
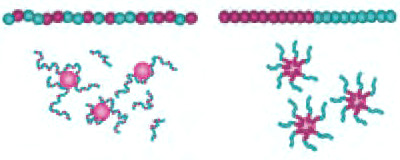
A pilot plant for living radical polymerization method with organic catalyst