Research Results
Technology that improves functionality and design
New welding method for spectacle frames FY2017
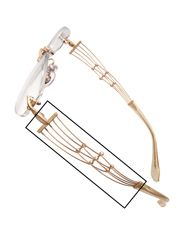
- Affiliation of project leader: CHARMANT Inc. / Researcher: Seiji Katayama (Osaka University)
- A-STEP
- Adaptable and Seamless Technology Transfer Program through Target-Driven R&D Seeds Development Type
High-quality and high-efficiency process technology for titanium alloy with the high-brightness laser adaptive control (2010-2013)
Limitations in spectacle design due to the difficulty of processing titanium
Titanium materials are often used to produce spectacle frames. Titanium offers many excellent advantages, including its lightweight property, high specific strength, corrosion resistance, biological safety, and flexible elasticity. These properties make it the ideal material for spectacle frames. The product development of spectacle frames started with the use of pure titanium, but gradually evolved over time to the use of titanium alloy and superelastic titanium alloy in pursuit of improvements in functionality in aspects such as strength and elasticity.
However, titanium is a material that is difficult to process. The processing techniques for processes ranging from pressing to milling, joining, and surface decorating, are all more difficult than iron and copper. For this reason, achieving advancements in processing technology that enables the joining of multiple parts in various ways has become an increasingly serious problem in embodying spectacle designs that are becoming ever more complex and diverse in recent years.
To that end, the research and development that fuses the high-quality precision welding technology using high-brightness laser, developed under Osaka University' s seed project, with the forging and blasting developed by the CHARMANT Inc., were selected under the Adaptable and Seamless Technology Transfer Program through Target-Driven R&D (A-STEP) program. This proj- ect enabled a significant reduction in the number of processes, as well as the practical application of highly functional spectacle frames of intricate design made from different types of materials, which was previously deemed too difficult to achieve.
Applying heat at pinpoints through laser technology
The joining of titanium spectacle frames mainly involves the use of the "resistance brazing method." In this method, parts a re brought into direct contact with electrodes, and they are subjected to pressure while electricity is passed through them. The resistive heat generated by the metal is used to melt the alloy (brazing), and the parts are then joined together. However, the brazing material used for titanium has a high melting point, and the brazing material must be spread out over the entire area to be joined in order to ensure that the joint is sufficiently strong. In doing so, heat effect is generated over a wide area, softening the material such that the frame becomes deformed easily. Fine precision laser technology is expected to provide the solution to this problem. Welding technology that uses fine precision laser is able to apply heat on focused areas through high-density light energy; hence, it is able to join parts directly without the use of brazing material, and without contact. In short, it is able to reduce the adverse effects of heat.
However, a serious problem arose during development. Generally, in laser welding, the width of the swell of the welding mark (weld bead) expands easily. To solve that problem, the diameter of the laser spot to be irradiated is reduced through the selection of a pulse in the laser device that is suitable for the fine joining work. Furthermore, by slowing down the welding speed (reducing the distance between pulse reps) and irradiating the laser beams close to one another, it became possible to reduce surface roughness and achieve a cleaner finish. In laser micro welding that does not make use of brazing materials, the precision of the gap between the parts to be joined and the accuracy of the position for laser irradiation are becoming increasingly important. Through strict process management, and by improving the precision of parts, precision of the welding jig, and precision in the positioning of the robots, overall welding precision was improved.
Through the development of this new technology, the team succeeded in reducing the number of the welding processes by 40% as compared to the previous process. It also succeeded in reducing the heat affected zone by as much as 88%, and made it possible to carry out welding without damaging the properties of new materials such as superelastic titanium alloy, which does not contain nickel, the cause of metal allergies. Furthermore, as it is possible to perform non-contact heating directly onto just the part that needs to be welded, it has become possible to weld various shapes including fine precision parts, thereby improving the degree of flexibility in design and functionality.

Schematic diagram of the conventional resistance brazing method (left, center) and its problems, and advantages of the laser micro welding (right)
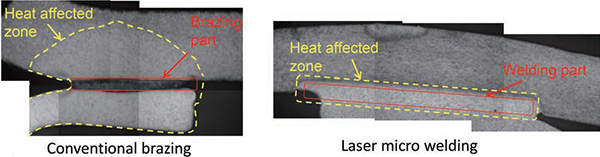
Comparison of heat affected zone for the welded part using the conventional brazing (left) and laser micro welding (right)
Newly added value of the spectacle frames
Under the A-STEP program of JST, laser welding technology through this adaptive control, and cold forging technology for titanium using a Servo Press, which allows the speed and position of the pressing process to be changed freely, have been fused to achieve advancement in titanium processing technology.
The CHARMANT Inc. has made use of these new techniques to produce innovative products, including the "LineArt CHARMANT" series. The temple of this spectacle frame is made with the superelastic titanium alloy, "Excellence Titan." Using laser micro welding to join wires of diameter 0.65 mm while minimizing the area of heat effect, the company has succeeded in producing it at a high level of precision without losing the property of superelasticity. Furthermore, the structure that combines thin wires provides the wearer with a level of lightness and comfort never experienced before.
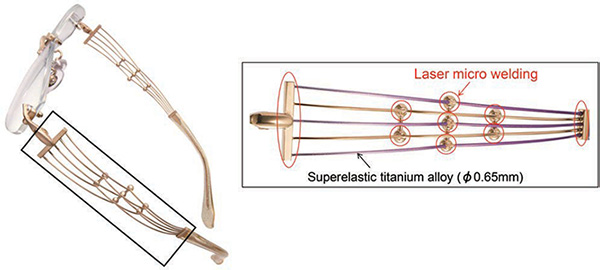
Commercialized spectacle frames made through laser micro welding
Success in creating highly-functional medical equipment products, and contribution to the local economy
The laser micro welding technology that has been developed bonds multiple materials of different varieties at the right places in the right way, creating a high level of functionality. It has also been applied to the production of new medical devices. For example, the needle holder, which is an instrument used in ophthalmic surgery, was successfully created by combining a unique titanium alloy with strong durability and hardness, used at the edge to hold the needle in place, with pure titanium that is easy to process used for the handles, and a titanium alloy that is flexible (low Young' s modulus) yet strong, used at the rear end of the holder. This combination of materials enabled accurate instrument operation during surgery, thanks to the reduction of burden of opening and closing the instrument, as well as improved responsiveness.
Entry into the medical sector is highly anticipated to have the effect of revitalizing the local community of Fukui Prefecture, where there is a concentration of precision processing technology for titanium. Of these, the CHARMANT Inc. plays a central role as a corporation that connects dealers of medical equipment with doctors in hospitals, as well as production sites. In this way, it contributes to the development of the local economy.
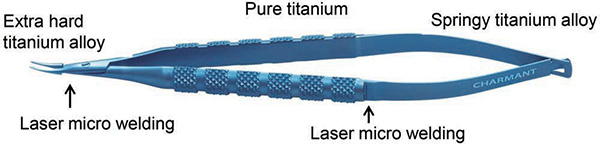
Ophthalmic instrument (needle holder)