Research Results
Tough but Easily Degradable into the Original Material
Development of a Polymer Material that can be Recycled without DeteriorationFY2024
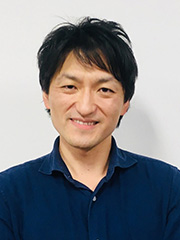
- SUZUKI Daisuke (Professor, Graduate School of Environmental, Life, Natural Science and Technology, Okayama University)
- CREST
- Research Director (2021–2026), Degradation and Stability Area: "Sustainable Polymeric Particle-based Materials with Mechanical Stability and Selective Degradability"
Establishment of a polymer material recycling method and the development of a new material
Polymer materials,*1 such as plastics, rubber, and textiles, are widely used in our daily lives. The research group led by Professor Daisuke Suzuki established a new recycling method that prevents the properties of polymer materials from deteriorating due to recycling.
The research group discovered a polymer film, formed by polymer chains-based microparticles that are several tens to several hundreds of nanometers in size, that is tough and highly degradable (Fig. 1).
By introducing rotaxane molecules*2 into polymer microparticles, they also succeeded in developing a microparticle-based polymer film, which is conventionally produced using organic solvents*3 and other additives to make them stronger, as a polymer material that is highly elastic and less liable to crack.
This microparticle-based film can be degraded into its original microparticles merely by dipping it into a mixed solvent of ethanol and water, and it can be used repeatedly without degrading in quality due to recycling.
*1 Polymer material
A compound made of a collection of many monomers. It may also be referred to as simply a polymer ("poly" means "many"). Monomers or low-molecular materials undergo a reaction (polymerization) to form a polymer.
*2 Rotaxane molecule
A molecular aggregate in which an axle molecule penetrates through a ring molecule. It is also called a molecular machine because of its mechanical link structure.
*3 Organic solvent
A solvent containing a thinner or the like. Organic solvents released into the air may cause photochemical smog and other environmental problems. When taken into the body in large amounts, they may cause headaches or dizziness.
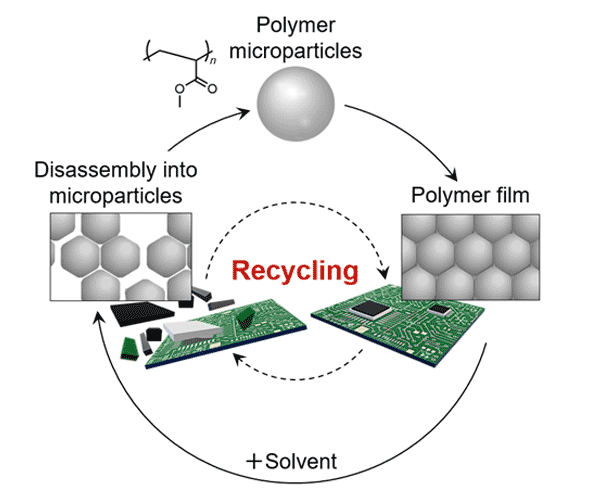
Fig. 1 Production of a tough film using polymer microparticles and their recycling
The urgent issue of solving social problems related to plastic waste
While polymer materials such as plastics, rubber, and textiles are now commonly used throughout to improve our daily lives, they also pose problems such as environmental pollution and resource depletion. As their production and usage increase, the amount of these materials that is wasted has also been increasing greatly. It is said that the amount of plastic waste released into the oceans alone totals several million tons per year, and its impacts on the environment and ecosystems have become a serious problem. Therefore, we must not only use quality products longer but also efficiently recycle and reuse them.
Existing polymer recycling methods employ chemical reagents and high-pressure-high-temperature processing to cause a degradation reaction to degrade the polymer materials into their raw materials or low-molecular materials (monomers).
Polymer microparticles that are several tens to several hundreds of nanometers in size, a key feature of this research, are common microparticle materials used in cosmetics and coatings as well as paper processing and other processing. It has been previously known that when water containing these microparticles is evaporated, the microparticles fuse to one another to form a microparticle-based film, and microparticle-based films produced by this method are commonly used in adhesives, coatings, and other products. However, the interfaces (bonding surfaces) between microparticles in a microparticle-based film tend to become a rupture point,*4 and the fragility of these materials is an issue.
Meanwhile, it is also known that microparticle-based films can be used as strong materials by reinforcing the interfaces, which may become a rupture point, by adding an additive or other measures. For example, natural rubber used in rubber gloves and other products is an aggregate of polymer microparticles, and it is used as a strong, elastic material by adding an additive to enable microparticles to bond to one another through a physical or chemical link in the particle interfaces. However, it is not easy to disconnect the interfaces once such a link has been formed, and trying to disconnect these interfaces by force may cause breakage or deterioration in unexpected locations. Thus, it has been difficult to recover these materials in a reusable form. It was thought to be difficult to reuse quality microparticle-based films even if the materials could be recovered because their quality would deteriorate in the recovery process.
In response to these issues, the researchers in this research have worked to develop stable, tough, highly degradable and recyclable polymer materials without using chemical raw materials.
*4 Rupture point
The point in an object at which it ruptures (or breaks) when force is applied.
A tough and highly degradable polymer material
In this research, the following results were obtained using a microparticle-based film made only of polymer microparticles.
① Establishment of a closed loop recycling method using polymer microparticles
It was discovered that a tough microparticle-based film can be formed using synthetic polymer microparticles made of a raw material for polymer materials widely used in adhesives, coatings, and other industrial products (methyl acrylate, which is an acrylate-based monomer). This film is made simply by drying a solvent containing the microparticles but has been found to be as strong as natural rubber with the particle interfaces reinforced. When the film's structure was observed with a special microscope, it was found that the polymer microparticles had closely fused to one another in the interfaces during the drying process, and this was identified as the key factor behind the film's toughness.
This microparticle-based film can be degraded into microparticles of the original size merely by dipping it into a mixed solvent of ethanol and water. By eliminating the ethanol, which has a low boiling point and is highly volatile, from this solution, polymer microparticles can be recovered in the form they were in before forming the film with them (Fig. 2).
The material recovery rate of this recycling method is as high as 99%, and the recycled film has the same performance as that prior to recycling. It was thus confirmed that a closed loop recycling*5 method has been established.
*5 Closed loop recycling
A recycling method of recycling an unnecessary product into a similar product. This method is highly sustainable because it leads to efficient use of limited resources and waste reduction.

Fig. 2 Cycle of formation and degradation of a microparticle-based film
This film can be degraded merely by dipping it into a mixed solvent of water and ethanol and can be recycled with no quality deterioration.
② A polymer material with improved safety and durability
By introducing rotaxane molecules into polymer microparticles, a microparticle-based film (rubber material) that is highly elastic and less liable to crack was developed without using additives or organic solvents.
This rubber material can be produced merely by evaporating water in a colloid solution*6 in which polymer microparticles are dispersed in the water, and it is highly resistant to cracking despite not using any additives or organic solvents. When a standard microparticle-based film is scratched and pulled, the scratch develops into a crack, which continues to widen, and the film tears. On the other hand, this microparticle-based film, which is highly elastic, does not allow cracks, if any develop, to widen easily (Fig. 3). This is the first film that is made of polymer microparticles without using additives and that has these characteristics.
The key factor behind this phenomenon is the rotaxane molecules used in designing microparticles (Fig. 4). A rotaxane molecule has a structure in which an axle molecule penetrates through a ring molecule. When rotaxane molecules are introduced into microparticles, they can be intertwined closely with one another in the bonding surfaces between them. This microparticle-based film can also be recycled without quality deterioration merely by dipping it into a mixed solvent of ethanol and water as described in ①.
*6 Colloid solution
A colloid is a generic name for materials in which polymer microparticles or other microscopic substances are dispersed in a liquid, solid, or gas. The colloid solution here is a water-based colloid in which microparticles are dispersed in water.

Fig. 3 Rubber material that elongates in a way that prevents cracks from widening
A tough microparticle-based film in which cracks resulting from cuts do not widen easily was developed.

Fig. 4 Process of forming a microparticle-based film
Polymer microparticles into which rotaxane molecules comprised of a ring and an axis are introduced are used.
Aiming to realize the ideal recycling society
The closed loop recycling method established in this research does not require a chemical reaction for degradation and its processes do not generate harmful substances. This method enables polymers to be used as raw materials longer as well as to be recycled and reused safely.
It is thought that as the research advances, this method will become applicable to various polymer materials beyond the one used in this research. The spread of such polymer materials is expected to help realize the ideal recycling society in which the highly functional products around us can be recycled after use.
In addition, polymer materials that do not use any additives may be usable as biomaterials in the human body and can be expected to produce other ripple effects.