Research Results
Efficient and energy-saving next-generation manufacturing
Development of an exhaust gas abatement tool for device manufacturing equipmentFY2023

- Development and implementation company
Kanken Techno Co., Ltd.
Principal Researcher
ICHIKI Takanori, Professor of Graduate School of Engineering, The University of Tokyo - Adaptable and Seamless Technology transfer Program through targetdriven R&D (A-STEP)
- "Highly efficient detoxifier using low-pressure plasma" (2017-2020), Industry-led phase NexTEP-A type
Efficiently detoxifying gases necessary for device manufacturing
Hazardous gases with toxic and flammable properties, such as monosilane and hydrogen, are used in manufacturing processes for semiconductors, flat panel displays, solar cells and other high-precision electronics products. Kanken Techno has developed a "abatement tool" based on research conducted by Professor Ichiki of the Graduate School of Engineering, the University of Tokyo, to efficiently abate hazardous gases used in electronics product factories.
Abatement of monosilane gas and hydrogen gas, which consume a huge Nitrogen dilution
Electronics products such as semiconductors, flat panel displays and solar cells make our lives fulfilling and convenient. In manufacturing plants for these products, the process of forming thin films on silicon and glass substrates is repeated to perform extremely fine processing. Hazardous gases with toxic and flammable properties, such as monosilane (SiH4) and hydrogen, are used, which cannot be released into the atmosphere, thus requiring the installation of a "abatement tool" to render them harmless.
Thermal oxidation reactions to decompose hazardous gases by heating them to approximately 1,000°C or higher are the major methods used to make them harmless. The specific example of monosilane gas, which is widely used in the chemical vapor deposition (CVD)*1 process for semiconductors, is described below. Monosilane gas reacts explosively just by contacting air at concentrations of 1.3% or higher, which is the lower explosive limit (LEL)*2. Monosilane gas is therefore diluted more than 75 times by nitrogen gas to prevent explosions. This process requires a huge amount of energy to heat massive amounts of exhaust gas to a high temperature due to dilution. Although "development of means to efficiently heat exhaust gas" and "development of a reactor structure to reduce waste energy by suppressing heat dissipation" have been carried out, there have been no major technological developments to realize energy conservation.
*1 Chemical Vapor Deposition (CVD)
It is one of the synthetic methods used to fabricate thin film materials, in which raw material gases containing the elements constituting the thin film are supplied to a reactor, and decompose and chemically react on a substrate to deposit a thin film thereon.
*2 Lower Explosive Limit (LEL)
Flammable gases or vapors of flammable liquids, when mixed with air or oxygen, explode in the presence of an ignition source within a specific gas concentration range. This concentration range is called the explosion range, with the lower concentration limit referred to as the lower explosive limit, and the higher limit as the upper explosive limit.
Finding optimal processing conditions to abate gases
In this development, attention was paid to the fact that the lower explosive limit of a combustible gas depends on its pressure, and pressure conditions that can reduce the amount of dilution gas were examined. However, little pressure-dependent data on the lower explosive limit of flammable gases is commonly available, with only a few examples of the reaction between hydrogen and air being studied on the high-pressure side. Kanken Techno, which was in charge of the development, accumulated data on various gases on its own.
In a conventional detoxifier system (Fig. 1), when hazardous gases are discharged from device (semiconductor, etc.) manufacturing equipment using a pump, they are diluted with nitrogen gas and then heated to high temperatures under atmospheric pressure to render them harmless. The new prototype abatement device (Fig. 2) uses a vacuum pump to reduce the pressure (approximately 10 kPa) from the pump outlet where toxic gases are discharged from the manufacturing equipment to the inside of the waste gas treatment equipment, thereby raising the lower explosive limit of the gas in the piping and creating an environment where no chemical reaction can occur, making dilution with nitrogen gas unnecessary. In addition, the high-temperature heating method used to decompose and detoxify hazardous gases was changed from a fuel combustion method to a plasma method. To realize the plasma method, optimal conditions were found that could stably generate arc plasma even at a reduced pressure of 0.1 to 10 kPa, which is normally generated at atmospheric pressure (101.3 kPa on the ground) (Fig. 3). This makes it possible to detoxify hazardous gases by thermally reacting them with oxygen using an arc plasma heat source in a reduced-pressure exhaust gas treatment system. Further, in order to prevent "by-products generated during detoxification from adhering to the inner walls of the reactor", which is a problem in actual waste gas treatment, a system for rinsing the inside of the reactor with water has been incorporated.
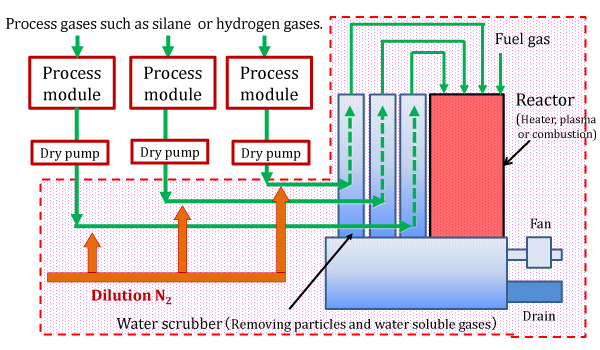
Fig. 1 Example of conventional atmospheric pressure detoxifier configuration
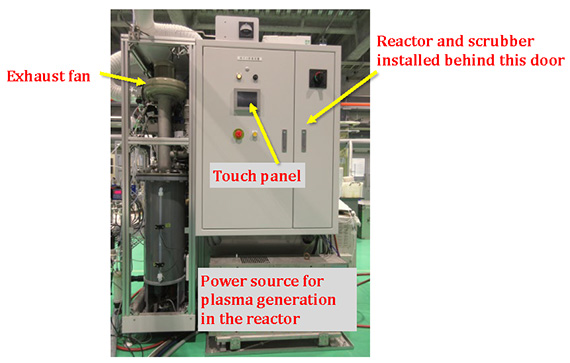
Fig. 2 Prototype low-pressure detoxifier
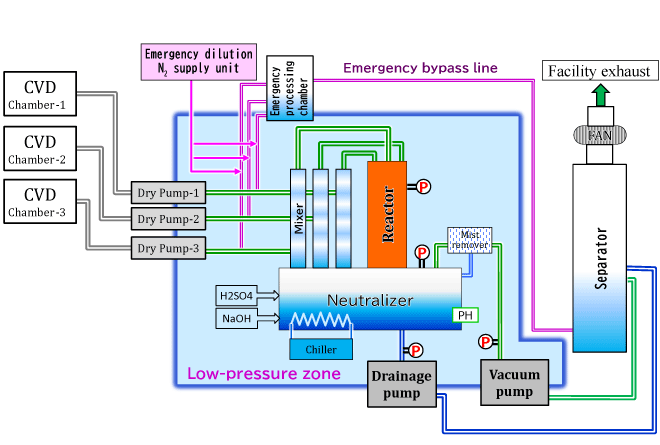
Fig. 3 Configuration of the new low-pressure detoxifier
Applications to a wide range of manufacturing equipment using hydrogen now in progress
The new detoxifier significantly reduces the use of nitrogen gas used in large quantities in manufacturing processes in the electronics industry. The elimination of the use of nitrogen gas for dilution has a particularly significant effect on CVD processes using silane gas, which are in operation in many plants.
Energy-saving benefits are also expected to be significant. Since no dilution by nitrogen gas is necessary, the total gas flow rate into the detoxifier decreases by a factor of 50 to 100, reducing energy consumption for exhaust gas treatment by approximately 75%. Semiconductor wafer sizes as well as monitor display sizes have been increasing recently, resulting in the use of larger quantities of silane-based gases in manufacturing processes. The more the amount of nitrogen gas to be reduced, the greater the effect of cost and energy reductions. This technology has already been attracting many inquiries as a means to significantly reduce the energy consumption of exhaust gas treatment, and is expected to be installed by semiconductor manufacturing companies.
In addition, the new technology can easily be applied to flammable gases other than silane gas that require nitrogen gas dilution by optimizing the treatment conditions, and without changing the configuration of the equipment. For example, it is expected to be applied to manufacturing equipment using hydrogen, such as hydrogen processing equipment for semiconductor silicon wafers, epitaxial growth*3 equipment, and ashing*4 equipment for organic films.
*3 epitaxial growth
One of the techniques to grow a thin-film crystal (simultaneous increase in mass and volume of a single crystal). This technology is used for high-quality semiconductor wafers, etc.
*4 ashing
A process of vaporizing and decomposing a resin such as a photoresist (photosensitive resin used in fine processing of semiconductors) by irradiating radicals, ions, etc., to its surface. A plasma of such gases as oxygen or hydrogen is used.
- Environment and Energy
- Research Results
- Japanese