Research Results
Contributing to a Low-Carbon Society by Reducing Vehicle Weight
Development of Low-Temperature Joining that Preserves the Strength Characteristics of MetalsFY2023
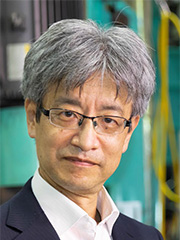
- FUJII Hidetoshi (Professor, Joining and Welding Research Institute, Osaka University)
- JST-Mirai Program
- "Low Carbon Society" Mission Area:
"Development of welding / separation integrated technologies by utilizing non-weldable materials", Project Leader (Feasibility Study, 2019-2024)
New methods of joining steel to steel desired from industries
Technology for welding and joining steel plates to steel plates is indispensable for various industrial products, including automobiles and railroad cars. Professor Fujii's research group has established "solid-phase resistance spot welding", which enables metal-to-metal joining in the solid phase (i.e., solid state), that was previously considered difficult, by incorporating elements of joining technology that have come to fruition as the "pressure-controlled Joule heat forge welding method*1" based on conventional "resistance spot welding*2.
Conventional "resistance spot welding" melts the material to be joined, so steel with high carbon content cannot be joined due to cracking. On the other hand, "solid-phase resistance spot welding" does not melt the steel and can be performed at low temperatures without changing its strength characteristics by applying high pressure and passing electric current through it.
If high carbon content steels can be successfully joined by "solid phase resistance spot welding", manufacturers will have a wider choice of materials to choose from. It also offers overwhelming advantages in terms of environmental impact, power consumption, and cost, leading to improved production efficiency. Further, since no oxides (spatter) of molten steel are produced in the welding process, this will lead to reduced post-processing removal costs in addition to improved quality.
Moreover, if innovative joining technologies such as "solid phase resistance spot welding" are put to practical use and dedicated materials, tools, and manufacturing equipment are developed, production activities and infrastructure construction with low CO2 emissions will come to be used all around the world, contributing to the realization of a low-carbon society (Fig. 1).
*1 Pressure-Controlled Joule Heat Forge Welding
A joining method that utilizes Joule heat produced by butt-welding the edges of the materials to be joined, and energizing them while applying pressure. By applying high pressure, the joining temperature can be kept at a low temperature at which the material does not change.
*2 Resistance spot welding
A method of spot welding of two metal plates by overlapping them, and applying pressure with a copper electrode while passing a large current through them to form a molten part due to the resistance heat generated in the metal, thereby welding the plates together.
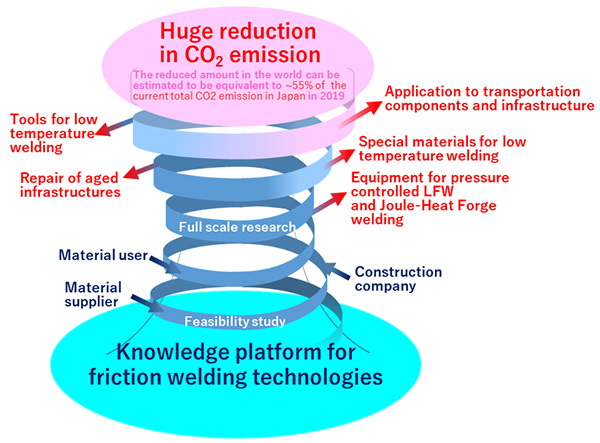
Fig. 1 Realization of a low-carbon society through practical application of innovative joining technologies
Conventional joining methods fail to maintain intrinsic strength characteristics
In the automotive industry, lighter and stronger materials are being developed to save energy by reducing the weight of car bodies. Steel is used as a material for most car bodies, but joining is not a simple technique. This is because the heat generated during welding causes phase transformations, which impair the original strength properties of the material. In this research, the group aimed to establish a new joining method that does not cause transformation of the material (steel) even when the temperature changes, based on "friction stir welding (FSW)" (Fig. 2), which is used as a joining technology for aluminum alloys in railroad vehicles and aircraft.
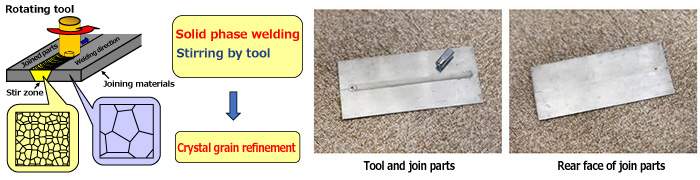
Fig. 2 Friction Stir Welding (FSW)
A method in which a rotating tool with a protrusion at the tip is pressed with strong force while rotating to cause the protrusion to penetrate, and the members are joined by frictional heat and the tool's rotational force.
Succeeded in low-temperature joining at about 700°C without strength loss of steel
In order to apply FSW, a process in which the rotation of a tool distorts the crystal structure of a material and the frictional heat generated recrystallizes it without melting, not only to aluminum but to steel, the research team explored the possibility of FSW at low temperatures. Steel has three phases with different crystal structures even in the same solid state, and when these phases change (transformation) due to temperature change, the steel becomes hard but brittle. As a result of exploring the possibility of FSW at lower temperatures, they succeeded in low-temperature welding at about 700°C, which was lower than the 1000-1200°C that had been the conventional wisdom for FSW. At about 700°C, the steel could be joined without phase transformation. However, FSW had cost issues compared to arc welding*3, which is currently the mainstream method, because the tools used for stirring are consumable. Therefore, in search of an even more efficient joining technology, they turned their attention to the old joining technology "linear friction welding (LFW)" (Fig. 3). By clarifying the relationship between "frequency and amplitude of vibrating metal plates" and "pressure applied from outside", which are variables for temperature control related to joining quality, they established their own joining technique, "Pressure-Controlled Joule Heat Forge Welding", and built a compact welding device prototype.
*3 Arc welding
A welding method that uses the electrical phenomenon called arc discharge to connect two identical metals.
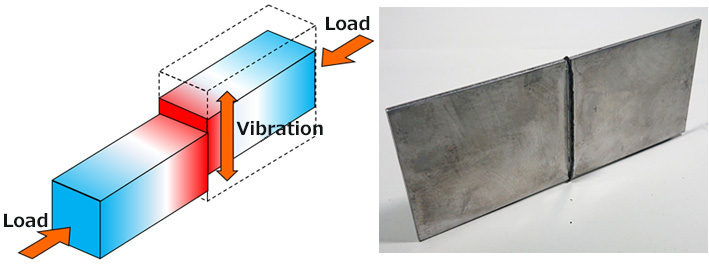
Fig. 3 Linear Friction Welding (LFW)
LFW is a method of joining materials by causing a linear motion of one of the materials to be joined while pressing them against each other, and joining them by the frictional heat of the joining surfaces. The photo on the right shows carbon steel materials joined together.
The feature of "Pressure-Controlled Joule Heat Forge Welding" is that it uses Joule heat generated by electricity instead of friction heat to raise the temperature of the joining surface in order to join two materials. When two metals are butted together and electricity is applied to them while pressure is applied from the outside, the temperature of the butted surfaces rise due to Joule heat, creating the same conditions as FSW and LFW. Since the higher the pressure, the lower the temperature, even steel can be joined without phase transformation. Further, in the prototype device, a metal shaft for pressurizing is installed separately from the electrode that conducts electricity to achieve the low-temperature joining that has been pursued for so long.
While based on conventional "resistance spot welding" or “cold spot joining”, the new technology is named "solid phase resistance spot welding" (Fig. 4) because it does not melt the materials to be joined, which would lead to their transformation, but joins them in the solid phase.
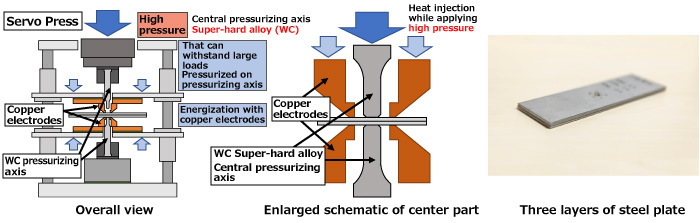
Fig. 4 Prototype incorporating "solid phase resistance spot welding"
A composite structure with a "copper electrode for energizing" and a WC (tungsten carbide) cemented carbide shaft for pressurizing has allowed the application of both high pressure and energization. The photo shows three steel plates joined by sandwiching high-tensile steel (high-tensile material) between cold-rolled steel plates (SPCC: Steel Plate Cold Commercial).
Aims for practical application in the automotive industry in collaboration with a major manufacturer
Through an industry-academia collaboration with DAIHEN Corporation, a leading manufacturer of welding machines and industrial robots, which has focused on the potential of the new "solid phase resistance spot welding", a prototype (Fig. 5) has been built, and efforts are underway to put it into practical use.
Approaches have also been made by domestic and foreign automobile manufacturers aiming to improve product quality and reduce the environmental impact of their production activities, and is expected to be adopted for use in the production of next-generation automobiles.
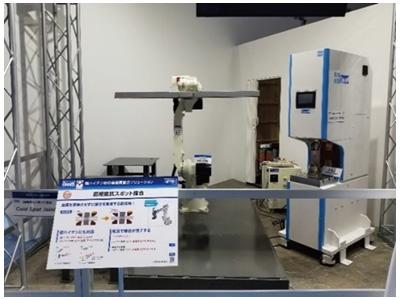
Fig. 5 "Solid phase resistance spot welder (Cold spot joiner)" prototype