Research Results
Significant energy savings in motors and transformers expected
Development of mass production equipment for thin magnetic ribbon, minimizing energy-lossFY2021
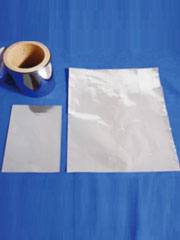
- Tohoku Magnet Institute Co., Ltd. /
Makino Akihiro (Professor, New Industry Creation Hatchery Center, Tohoku University) - Adaptable and Seamless Technology Transfer Program through Target-driven R&D (A-STEP)
- Company-led phase NexTEP-B type, "Production equipment for ultra-low loss nano crystal ribbon"
Company leading the development/Representative Researcher (2017 - 2019)
Succeeded in developing mass production equipment for magnetic ribbon that contributes to significant energy savings in motor power.
Magnetic devices such as motors, which convert electricity into power, and transformers, which convert voltages, lose electrical energy due to the use of iron and copper as materials for their components (called iron and copper losses, respectively). For this reason, research and development of new materials with low iron and copper losses is being carried out to improve the energy efficiency of motors and transformers.
"Silicon steel sheets", in which silicon is added to iron, have typically been used as electromagnetic steel sheets. With this background, Tohoku University Professor Makino's group invented a "nanocrystalline material" consisting of iron and a small amount of common elements as a magnetic material with magnetic properties comparable to silicon steel sheets, but with smaller iron loss. Tohoku Magnet Institute, a venture company from Tohoku University, was established in 2015 with the aim of commercializing this technology.
Then the company, with the support of the NexTEP-B type, in order to produce "ultra-low-loss nano crystal*1 ribbon" (Fig. 1), which is a thin strip of nanocrystalline material, succeeded in developing mass production equipment (Fig. 2). It started production in October 2019. If this new material is adopted for power motors in the future, it will be used in a wide range of products including electric vehicles. This will lead to significant energy savings in motor power, which is estimated to account for about half of the world's electricity consumption.
*1 Ultra-low loss nano crystal
This is a magnetic material with a high iron concentration containing 93 - 94% of iron by mass. It has a structure with an amorphous magnetic layer around nanocrystalline grains of alpha-iron (α-Fe) of about 10 nanometers. The amorphous magnetic layer consists of common elements such as silicon (Si), boron (B), phosphorus (P) and copper (Cu).
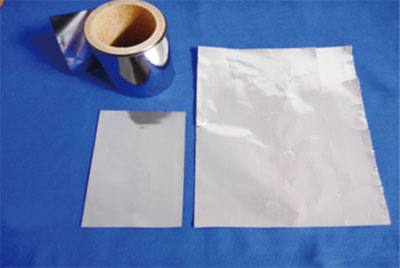
Fig. 1 "Ultra-low loss nano crystal ribbon" ready for mass production
The photo shows ultra-low loss nano crystal ribbons with widths of 127 and 245 mm produced by the newly developed equipment. These are mass-produced in the form of rolls.
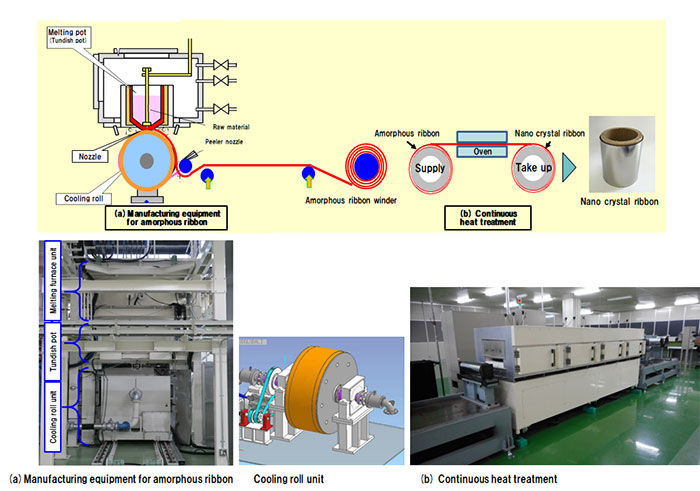
Fig. 2 Equipment for manufacturing ultra-low loss nano crystal ribbon
(Top) Overall configuration of the equipment. From left to right: (a) manufacturing equipment for amorphous ribbon, amorphous ribbon winder, (b) continuous heat treatment. (Bottom) From left to right: (a) view of manufacturing equipment for amorphous ribbon, and structure of cooling roll unit, (b) continuous heat treatment
Manufacturing equipment for amorphous ribbon developed based on A-STEP research results.
Although the ultra-low loss nano crystals developed by Tohoku University showed excellent performance, the technology for mass production of ribbon form had not yet been established. If mass production technology that enables high quality, low cost and stable production is available, it will meet the demand for a wide range of devices.
Therefore, the Tohoku Magnet Institute's first approach was to develop manufacturing equipment for amorphous ribbon. The design of the large-scale cooling roll and the specification of the intermediate vessel for stabilizing the molten alloy were based on computer simulations. The induction heating*2 capacity of the IH heater as the heating source and the cooling capacity of the cooling roll were also determined by simulations.
In this way, the manufacturing process consisting of continuous injection of molten material into a wide, thin sheet, followed by rapid cooling, and then winding into a roll as a long amorphous ribbon, which is then continuously annealed and cooled, was established. It was confirmed that the ribbon produced by this process had about one-sixth the iron loss of a typical silicon steel sheet (Fig. 3).
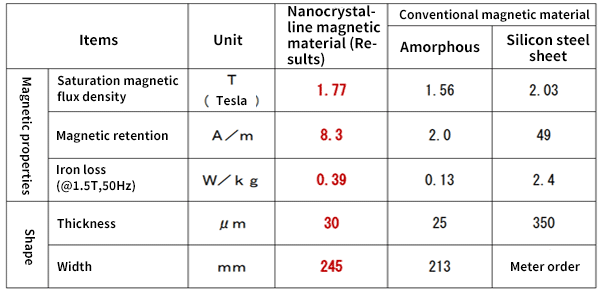
Fig. 3 Comparison between ultra-low loss nano crystal ribbon and conventional magnetic materials
Compared to a typical silicon steel sheet, the iron loss of the ultra-low loss nano crystal ribbon decreases to approximately one-sixth.
*2 Induction heating
This is a non-contact heating technique for electrically conductive materials (mostly metals).
Elemental technologies for reducing costs also developed.
On the other hand, the development of elemental technologies to reduce costs and prevent impurities from contaminating the material was also addressed. An innovative feature was the use of an upright crucible structure for the melting furnace. It allows 250 kilograms of raw materials to be completely dissolved within 60 minutes.
The conventional method of manufacturing a ribbon involves preparing a mother alloy with the components adjusted beforehand, and then melting it to form the ribbon. In this approach, however, the raw materials iron, silicon, boron, phosphorus and copper are directly fed into the manufacturing equipment for amorphous ribbon, followed by adjustment of the components in the melting furnace. This approach has helped to put the project on track to reduce material costs by approximately 90%. The extension of the life of refractories such as the crucible and nozzle was also examined. After selecting the most suitable materials and fabricating them, the durability was repeatedly tested on physical samples. Development of the manufacturing equipment incorporating these technologies led to the industry's first success in forming a 245 mm wide ribbon, and mass production is now on track.
Annealing equipment was also developed. The ribbon formed by the manufacturing equipment for amorphous ribbon acquires magnetic properties that meet the specifications by growing nanocrystalline grains through annealing. Accordingly, the annealing equipment incorporates technology that enables processing at four times the speed of conventional methods, based on information such as crystallization data obtained from the experimental equipment. The results show that the magnetic properties of the ribbon obtained meet the specifications required by prospective users.
Achievements available for a wide range of applications from home appliances to electric vehicles and industrial equipment.
It is estimated that motors account for about half of the electricity used in the world today, thus there is a need for highly efficient motors. The automotive industry, in particular, which is shifting to electric vehicles, has a high demand for this because reducing power loss is directly linked to the cruising distance. There is also a need for further energy savings in home appliances due to the large power consumption of refrigerators and air conditioners operating 24 hours a day. Energy savings in transformers for industrial equipment and infrastructure are a key issue as well. Applying the ultra-low loss nano crystal ribbon to these products will lead to significant energy savings.
The company plans to start full-scale production and sales of ultra-low loss nano crystal ribbons as well as to further improve quality, lower costs and enhance production stability. It thereby aims to contribute to the growth of Japanese industries.