Research Results
Contributing to the prevention of global warming
Succeeded in mass production of “solid-solution alloy nanoparticles" in which elements are mixed at atomic levelFY2021
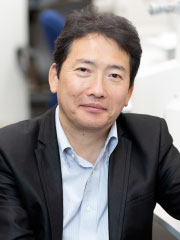
- Kitagawa Hiroshi (Professor, Graduate School of Science, Kyoto University)
- CREST
- Creation of Innovative Functions of Intelligent Materials on the Basis of Element Strategy "Creation of Functional Materials on the Basis of the Inter-Element-Fusion Strategy" Research Director (2011 - 2015)
- ACCEL
- "Creation of the Functional Materials on the Basis of the Inter-Element-Fusion Strategy and Their Innovative Applications" Research Director (2015 - 2020)
Mass production technology for innovative "solid-solution alloy nanoparticles" established.
Alloys with properties different from those of a single metal have been created and used by mixing several types of elements, mainly transition metals and typical metals among the elements that exist stably and are widely used all over the world, or by mixing nonmetallic elements such as carbon. Alloys are classified according to how the metal elements are mixed, and one of the states is "solid solution", in which the elements are mixed at the atomic level. On the other hand, many combinations do not mix and do not form a solid-solution alloy.
The research group led by Kitagawa Hiroshi of ACCEL has discovered that a combination of immiscible metals can be turned into a "solid-solution alloy" mixed at the atomic level, and has been studying the mechanism of solid-solution formation, searching for new functions, and developing new solid-solution alloys based on theoretical predictions. Professor Kitagawa and the research group of Furuya Metal Co., Ltd. announced in September 2019 that they have succeeded for the first time in the world in establishing a mass-production technology capable of continuously and stably synthesizing solid-solution alloy nanoparticles of a controlled size of about one nanometer, which had previously been considered difficult. This brings us one step closer to practical use of solid-solution alloy nanoparticles. Making solid-solution alloys of immiscible combinations not only makes it possible to create materials with new functions, but also to achieve better functions by controlling the particle size to the nanometer level.
They had also carried out studies to create and ensure the stable existence of solid-solution alloys with combinations different from previous studies that show new functions, and announced in August 2020 that they had succeeded in synthesizing "platinum-group-metal high-entropy-alloy nanoparticles (PGM-HEA)*1" (Fig. 1), which is a homogeneous mixture of all six platinum-group elements at the atomic level, and that the PGM-HEA shows an extremely high catalytic activity not found in conventional metal catalysts.
*1 high-entropy-alloy (HEA)
There are various definitions, but this is a solid-solution alloy in which the entropy of mixing was increased by mixing multiple components of five or more elements in roughly equal amounts.
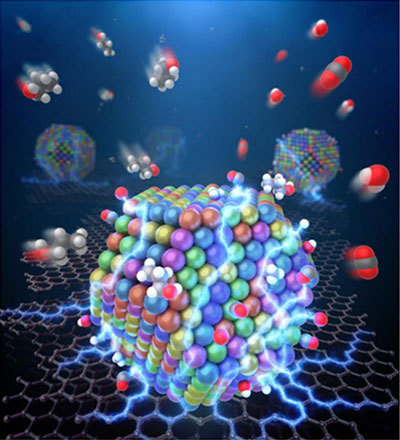
Fig. 1 Illustration of platinum-group-metal high-entropy-alloy nanoparticles (PGM-HEA)
Succeeded in the synthesis of highly active PGM-HEA, which is a homogeneous mixture of all six platinum-group elements at the atomic level.
One-nanometer level solid-solution alloy nanoparticles with uniform quality continuously synthesized.
The "liquid-phase reduction method" is a common method for synthesizing solid-solution alloys but the reduction rate and time, which are keys to controlling the size and uniformity of solid-solution alloy particles, have been difficult to control in the past. The manufacturing system (Fig. 2) developed by Kitagawa's group, which applies the "solvothermal synthesis method*2", can simultaneously control the reduction and cooling rates of metal atoms under high temperature and high pressure, and can continuously synthesize one-nanometer level solid-solution alloy nanoparticles of uniform quality (Fig. 3).
Metal nanoparticles (of several nanometers or less in diameter) are known to show unique properties not found in bulk materials, and controlling the particle size is an important factor in achieving good performance for solid-solution alloy nanoparticles.
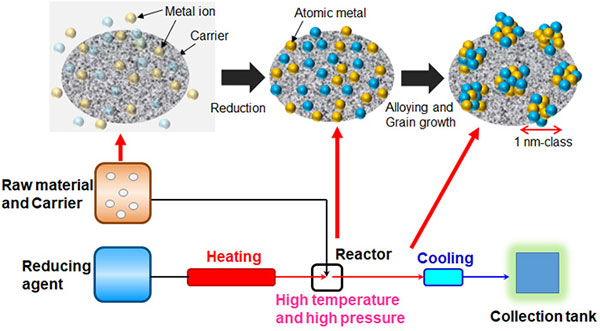
Fig. 2 Conceptual illustration of the production of solid-solution alloy nanoparticles using the solvothermal synthesis method.
Highly dispersing raw materials and carriers (materials that serve as a foundation for fixing active catalyst particles, etc.) in a solution and mixing them with a high-temperature reducing agent under high pressure produces reduced metal particles on the carriers. The mixture is rapidly cooled to prevent particle agglomeration and to produce catalysts with one-nanometer level solid-solution alloy nanoparticles supported on the carriers.
*2 solvothermal synthesis method
This is a method of synthesizing solids using high-temperature or high-pressure solvents (or supercritical fluids).
In the "liquid phase reduction method", a polymeric protective agent is necessary to keep the solid-solution alloy nanoparticles stable and nanoparticulate without agglomeration, but it is also known that a protective agent reduces catalyst performance. This system enables the reduction and the supporting of the catalyst on the carriers at the same time by simultaneously flowing the metal solution and the catalyst carrier slurry, thus making it possible to synthesize a catalyst with higher catalytic activity supporting one-nanometer level solid-solution alloy nanoparticles without using such a protective agent.
-
Nanoparticles on carriers
-
Element distribution image
(Each element is indicated by a color)
Fig. 3 Catalysts supporting solid-solution alloy nanoparticles (high-angle annular dark-field scanning transmission electron microscopy images)
These images show the solid solution state of the Pt-Ru-M alloy (M is the third metal added). These are solid-solution alloy nanoparticles of 1 to 2 nm supported on carriers of 10 nm in size. The three elements are indicated by red, blue and green, and particles that are completely homogeneously mixed by white in the element distribution image.

Fig. 4 Difference from the conventional method
The new method can simultaneously control the reduction of metal atoms and cooling rates under high temperature and high pressure. As a result, it can continuously synthesize one-nanometer level solid-solution alloy nanoparticles of uniform quality.
The synthesized alloy nanoparticles are being considered for practical use as catalysts. Rhodium (Rh) has the best catalytic activity to remove nitrogen oxides in exhaust gas. It was found that the Rh solid-solution alloy nanoparticles synthesized by this method are cheaper than Rh alone due to their low Rh content, and they also show high catalytic activity at low temperatures of about 50 °C. Moreover, the alloy shows more than seven times higher catalytic activity against nitrogen oxides than Rh at 160 °C (Fig. 5).
The system has also successfully synthesized solid-solution alloy nanoparticles containing 3d transition metal elements, which are considered difficult metals to reduce, due to the fact that the system enables synthesis under a high temperature of 450 °C and high pressure of 30 MPa.
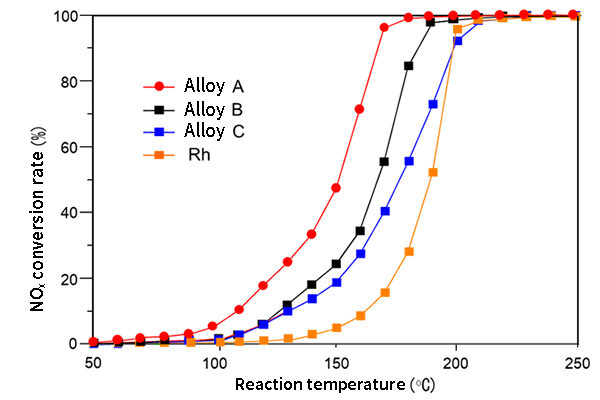
Fig. 5 Comparison of nitrogen oxides (NOx) removal performance
Alloys A and B are solid-solution alloys of three elements including Rh, and Alloy C is a solid-solution alloy of two elements including Rh. They show high activity in such a way that the NOx conversion reaction proceeds at a lower temperature than Rh alone. The reaction starts at a lower temperature in alloy A than in Rh alone. It has a NOx conversion rate of more than seven times that of Rh at 160 °C.
Creation of new materials: PGM-HEA, a homogeneous mixture of all six platinum group elements at the atomic level.
Professor Kitagawa's studies on solid-solution alloys have been based on the idea of "inter-element fusion". The origin of the idea was that it might be possible to find another element with intermediate properties between an element shown in the periodic table and the next neighboring element. The "non-equilibrium chemical reduction method" is an effective synthetic method, bringing a non-equilibrium state created under extreme conditions such as high temperature and high pressure back to ambient temperature and pressure in a short time, and is a way to create new materials by mixing materials that are immiscible in the equilibrium state. They have also shown, by performing theoretical analysis, that increasing the configurational entropy by increasing the number of elements in the mixture can thermodynamically stabilize the unstable non-equilibrium state in the system with the additional third element. They had been synthesizing solid-solution alloy nanoparticles of three or more elements and exploring their functions, and in August 2020, they successfully synthesized the world's first platinum-group-metal high-entropy-alloy nanoparticles (PGM-HEA), which is a homogeneous mixture of all six platinum-group elements (platinum (Pt), palladium (Pd), Rh, iridium (Ir), ruthenium (Ru) and osmium (Os)) at the atomic level (Fig. 6).
They examined the ethanol oxidation reaction activity of the PGM-HEA they created. The ethanol oxidation reaction is a 12-electrons reaction with complete oxidation, as described by CH3CH2OH + 3H2O = 2CO2 + 12H+ + 12e−, in which the reaction stops halfway due to the promotion of a four-electron reaction producing acetates, and poisoning by CO byproducts is a problem with conventional metal catalysts (e.g., Pt and Pd). The catalyst that has been considered to have the highest catalytic activity, Au@PtIr/C,*3 promotes a 12-electrons reaction, but PGM-HEA promotes a 12-electrons reaction as well and has high catalytic activity, and is 2.5 to 30 times more active than monometallic catalysts of each metal in the mixture. No activity degradation due to CO byproducts was observed, indicating that the catalyst has both high activity and high durability (Fig. 7). It is suggested that the surface is rich in adsorption sites consisting of six elements, and that C-C bond cleavage and oxidation of C1 components are concertedly occurring at each adsorption site.
*3 Au@PtIr/C
This catalyst, which was published in the Journal of the American Chemical Society in 2019, is a carbon-supported catalyst with PtIr attached to a core Au particle as a shell.
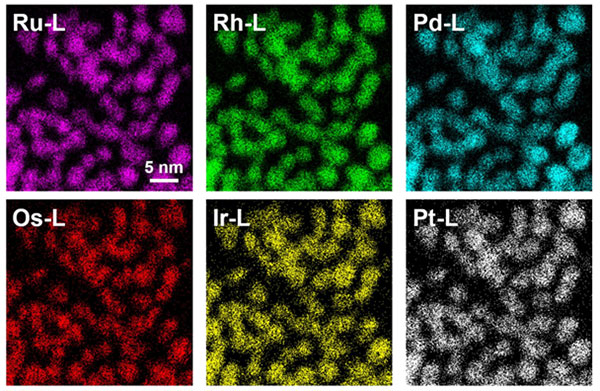
Fig. 6 STEM-EDS (scanning transmission electron microscope-energy dispersive X-ray spectroscopy) map of PGM-HEA
All six elements of the platinum group (platinum (Pt), palladium (Pd), rhodium (Rh), iridium (Ir), ruthenium (Ru) and osmium (Os)) have been successfully mixed. The map shows that all six elements are uniformly present in each particle.
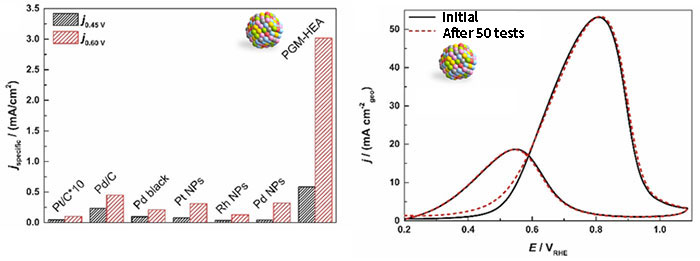
Platinum group multi-element alloy nanoparticles show extremely high catalytic activity for ethanol oxidation, high durability, and CO poisoning resistant property.
Fig. 7 Catalytic properties of ethanol oxidation reaction: (left) comparison of current density at 0.45 V and 0.60 V, (right) evaluation of the durability of PGM-HEA by cyclic testing.
For application in various fields such as catalysts, electronic and magnetic materials.
The establishment of a production method based on the solvothermal synthesis method, which enables the control of particle size in the nanometer range, has enabled the stable production of solid-solution alloy nanoparticles, and this synthesis method has greatly expanded the variety of alloys that can be synthesized. Since it has become possible to continuously control a wide range of properties, it is expected to meet the demands in the wide field, including electrocatalysts, chemical process catalysts, electronic materials such as quantum dots and magnetic materials, as well as the exhaust gas cleaning catalysts that are already being studied. Furthermore, the use of HEA as a catalyst has only begun, and it has the potential to become a dream catalyst that offers both high activity and high durability for complex and highly challenging catalytic reactions that cannot be achieved with conventional metal catalysts. Professor Kitagawa is expected to lead the research to discover new solid-solution alloy materials with high performance in the future.