Research Results
The Key to a Low Carbon Society
Strong, light weight, and inexpensive “magnesium alloy”FY2020
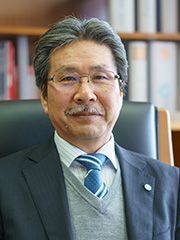
- Shigeharu Kamado(Professor, Nagaoka University of Technology)
- ALCA
- Enabling Technology Project「Innovative Light-Weight Materials for the Forward Energy-Saving Society」
「Innovative Development of Strong and Formable Wrought Magnesium Alloys for Light-Weight Structural Applications」(2012-2019)
The next generation “magnesium alloy”: an alternative to aluminum alloy
Presently, “aluminum alloys,” which are both strong and lightweight, are being widely used as structural materials for transportation vehicles such as the bullet trains (the Shinkansen), automobiles, and airplanes. However, if the weight can be further reduced, fuel efficiency in terms of transportation will be improved and the emission of carbon dioxide (CO2) can be drastically reduced. To that end, the practical use of “magnesium alloy,” the lightest among practical metals with a specific gravity two-third that of aluminum alloys, is highly anticipated. Though its use for computers and camera frames is expanding, there is an issue with strength and workability at room temperature, and its application in the field of transportation has not progressed.
Professor Kamado Shigeharu, the research and development representative of ALCA, succeeded in developing revolutionary magnesium alloys with strength and workability/formability equivalent to existing steel and aluminum alloys. Its strength exceeds aluminum alloys that are currently used for the body of Shinkansen/automobiles.
The ultimate goal for practical use is to apply it to a wide range of transportation vehicles. As the first step, development for application as automobile parts is in progress.
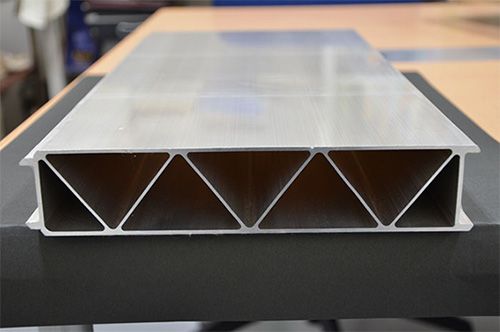
Figure 1. The newly developed magnesium alloy. A prototype Shinkansen model created by high-speed extrusion.
Balancing strength and workability through “Guinier-Preston zone”
Traditional magnesium alloys are made with mold casting called die casting, where alloy melted at high temperature is poured into a mold and cooled. However, this process does not provide sufficient strength.
Processing methods that improve strength include extrusion and rolling. However, existing magnesium alloy has poor workability/formability. When extruding, the extrusion speed of magnesium alloy is less than half that of the aluminum alloy with moderate strength known as the “6000 series,” which is used for sashes in construction and the body of vehicles. Therefore, mass production is not possible.
Professor Kamado designed a magnesium alloy with small amounts of aluminum, manganese, and calcium to achieve strength and workability equivalent to the 6000 series aluminum alloys. The key for this success was the “Guinier-Preston (G.P.) zone,” aggregate of atoms in the form of a thin layer with a thickness of one atom. Cast ingots are prepared by melting of magnesium and other elements at high temperature. When this material is extruded and placed in a 200°C environment for a certain period of time, the G.P. zone is created in the alloy and the strength is drastically increased. This phenomenon wherein a property of metal or alloy changes over time is called “aging.”
Professor Kamado successfully extruded a newly designed magnesium alloy at a high speed of 60 m/min in 2013. In addition, it was discovered that, by aging this magnesium alloy at 200°C for only 15 to 30 minutes, high number density of the G.P zones appeared and the its strength exceeded the 6000 series aluminum alloys that used for the body of a Shinkansen.
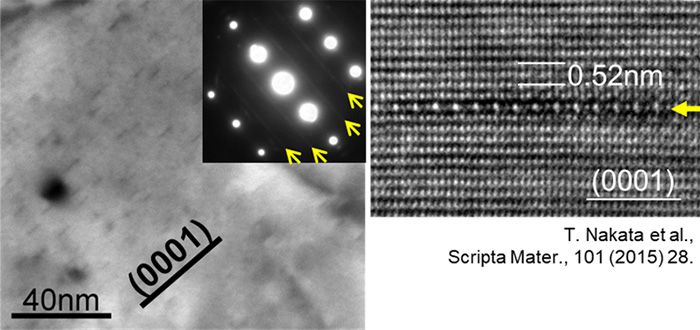
Figure 2. Precipitation of atomic aggregate “G.P. zone” in a form of thin layer, resulting in higher strength than that of the aluminum alloy used for the body of a Shinkansen.
By utilizing computer simulation, the alloy composition is forecast at nanometer and micrometer levels
Professor Kamado also developed rolled materials. In terms of the cost, it was required easily available elements to be used as alloying elements instead of expensive elements such as rare earth, and press forming can be performed at room temperature. When a small amount of zinc was added to the successfully extruded magnesium alloy, crystal orientation was controlled so that it could be formed in a round shape at room temperature like aluminum alloy sheets. This is because the addition of small amount of zinc changed the hexagonal prism orientation called a “hexagonal close-packed arrangement” and improved formability. In addition, he was first in the world to show that by aging for only 20 minutes at 170°C, which is equivalent to the thermal history for the body panel of an automobile, strength drastically improved.
As such, the properties of magnesium alloy change drastically by changing the ratio of alloying elements by a small amount. Therefore, Professor Kamado utilized various types of computer simulations to derive guidelines in searching for alloy systems that form the G.P. zone, and successfully simulated the growth of the G.P. zone. As the result, the composition of nanometer and micrometer structures could be forecast, leading to the present result. In addition, since the simulation results were consistent with experimental results, verification of G.P. zone formation became possible. The mechanism with which alloying elements contribute to improve strength was also clarified at the atomic level.
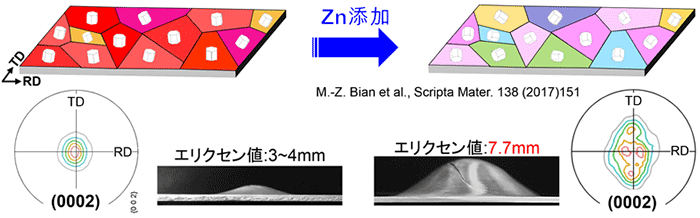
Figure 3. When a small amount of zinc was added to successfully extruded magnesium alloy, it could be formed into a round shape at room temperature, similar to aluminum alloy sheets.
The ultimate goal is application to trains and automobiles
In the future, professor Kamado will examine the types and amounts of elements that can be added to achieve desired properties based on the present results. In addition, through detailed computer simulations of microstructures formed during extrusion and rolling, proper thermal and aging processes along with correct temperature range of processing will be clarified and systematized. In this manner, the manufacturing process will be optimized with the ultimate goal being application to a wide range of transportation methods such as automobiles and trains.
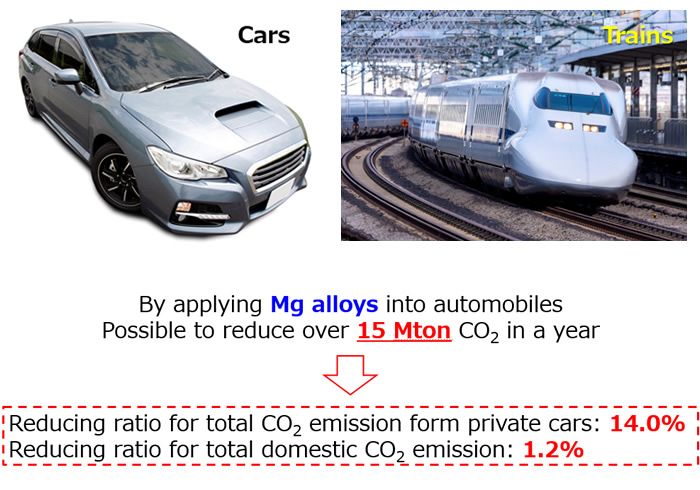
Figure 4. The ultimate goal is application to a wide variety of transportation vehicles such as automobiles and trains. In this manner, CO2 emissions can be drastically reduced.