Research Results
The application of “structural coloration” from Japanese gold beetles
Ultra-High-Definition Printing Achieved by “Cracks” and “Light”FY2020
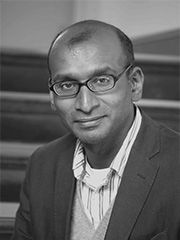
- Easan Sivaniah(Professor, Institute for Integrated Cell-Material Science(iCeMS), Kyoto University)
- PRESTO
- Hyper-nano-space design toward Innovative Functionality「The virtual surface - the use of internal structure to alter external material properties」Researcher (2014-2017)
- START
- Project support type「Practical development research of new membrane filter using Collective Osmotic Shock method --Aiming to realize energy-saving and low fouling (membrane fouling) membrane」Research Director(2014-2017)
- A-STEP
- StageII(Seeds development type)Third field「Development of charge gas reforming technology for ultra-high efficiency automobile engine」Research Director(2015-2017)
- JST-Mirai Program
- Realization of a low-carbon society as a global issue Realization of a low carbon society through game changing technologies「Development of mixed matrix porous membrane endowed with high performance in CO2 selectivity and anti-aging」Research and Development Director(2017-2021)
Creating Color in Substances without Ink
PRESTO researcher, Professor Easan Sivaniah et al., has developed a coloration method that does not require ink, but instead creates color with artificial, sub-microscopic structures. So-called “structural coloration” is observed on the surface of Japanese gold beetles and the feathers of peacocks, producing vivid, bright colors. Instead of pigment, special multilayered structures reflect light to create color. The technology is inspired by this natural system. By adding fine, systematic coloration structures to the surface of a material, the substance itself yields color through its sub-microscopic shape, resulting in a method of picture-making that has never been seen before.
Previously, there was an application of structural coloration, but it required expensive materials for printing. In contrast, this newly developed method uses industrial polymer films of acrylic resin and polycarbonate that are exposed to lights such as LEDs. Then, dipping in solvents such as acetic acid will cause fine cracks to form, creating a multilayered structure that is colored by its complex interaction with light. Since expensive materials or special light emitting devices are not needed, it is useful for a number of applications going forward.
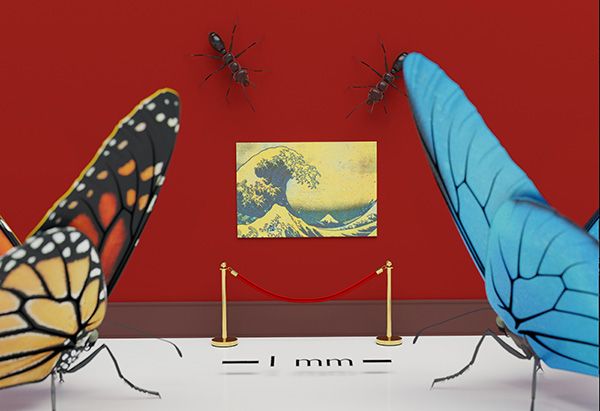
Fig. 1 A conceptual image: Structural coloration image admired by living organisms
Creating the Color Spectrum by Controlling Cracks
Repeatedly bending a transparent plastic ruler will cause its color to change to cloudy white. This happens because exposure to pressure causes the polymers to be stretched out at a molecular level, creating microscopic pre-cracks which is known as the “crazing” effect. When this occurs, fine fibers called “fibrils” are formed in the interior of the polymer. When crazing occurs enough, the high amount of fibrils causes the effect to be visible to the naked eye.
Since it causes damage to the material, crazing was formerly considered undesirable; however, by controlling the pressures and stresses within the polymer, and creating applying them in alternating layers of high and low stress, Professor Sivaniah and others succeeded in producing multilayered, porous craze structures within polymers. This multilayered, porous structure, shaped by artificial and systematically shaped fibrils, reflects the light of a different color depending on the spacing of the fibril crack layers. It is already capable of flexibly colorizing the surface of a range of transparent materials, with any visible spectrum color one wishes, from blue to red.
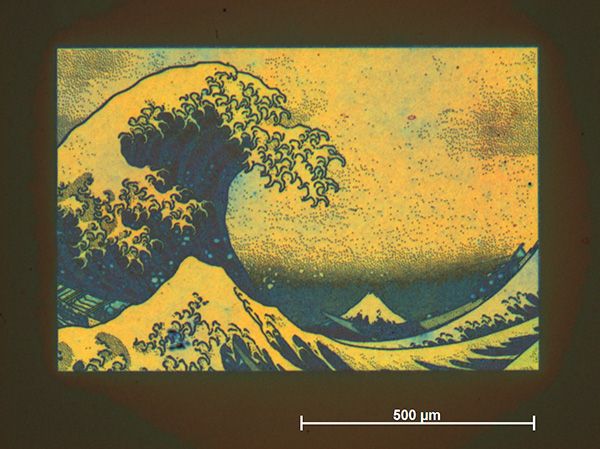
Fig.2 A picture printed in color without ink. The picture was drawn by the formation of multilayered structures through light exposure, creating color.
High Resolution Printing That Won’t Fade is Possible
This technology is called OM (organized microfibrillation) technology. Coloration through OM technology is controlled through the regular spacing of crack layers. The more cracks there are, the more vivid the resulting colors. Furthermore, it has demonstrated the capability of applying stress with a precision of less than 2 micron to form the microscopic cracks that cause structural coloration at high resolution.
Up to now, the maximum resolution achieved with OM is 14,000 dpi (the typical resolution for pictures printed on paper ranges from 350 to 400 dpi). This is an extremely fine level, through which large-scale, inkless printing is possible. Because ink is not used, the printed surface is less apt to fade. Moreover, because the fibrils themselves, the cracks in the polymer interior, are less susceptible to imitation, there are promising counter-forgery applications for things such as tickets and identification documents.
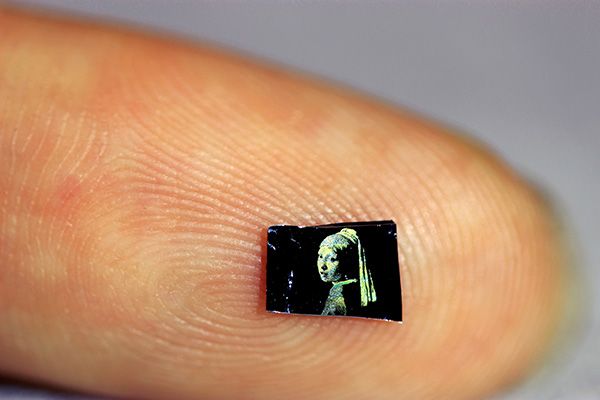
Fig.3 High-definition printing is possible even at a miniscule size. Vermeer’s “Girl with a Pearl Earring” printed with OM technology.
Medical and Healthcare Applications
Structurally, the cracks are hollow and interlinked over long distances. As a result, liquid can be circulated through the cracks, suggesting future medical and healthcare applications. OM technology could also be incorporated into medical devices that are placed on the body such as a flexible fluid circuit board or contact lens to transmit acquired biomedical information to the cloud or directly to your healthcare professional.
Also, it is predicted that the same controlling of cracks can be used in metal and ceramic materials, not just polymers. Going forward, we plan to research the regulation of cracks in these materials as well.