事業成果
効率的で省エネルギーな次世代型ものづくり
デバイス製造装置向け排ガス除害装置の開発2023年度更新
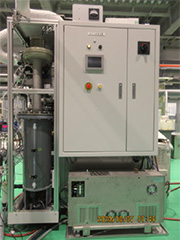
-
開発実施企業:カンケンテクノ株式会社
代表研究者:一木 隆範(東京大学 大学院工学研究科 教授) - 研究成果最適展開支援プログラム(A-STEP)
- 企業主導フェーズ NexTEP-Aタイプ「減圧プラズマによる高効率除害装置」 (2017-2020)
デバイス製造に必要なガスを効率よく無害化
半導体やフラットパネルディスプレイ、太陽電池などの精密なエレクトロニクス製品の製造工程では、シランガスや水素ガスなど毒性や可燃性を持つ危険なガスが使用される。東京大学大学院工学系研究科の一木隆範教授が行った研究を基に、カンケンテクノが開発した「除害装置」を用いることで、エレクトロニクス製品の工場で扱う危険なガスを効率よく無害化できるようになった。
多大なエネルギーを消費するモノシランガスや水素ガスの無害化処理
私たちの生活を豊かで便利にしてくれる半導体やフラットパネルディスプレイ、太陽電池などのエレクトロニクス製品。その製造工場では、シリコンやガラスの基板に薄膜を形成する工程が繰り返され、極めて微細な加工が行われている。また、モノシランガス(SiH4)や水素ガスなど、毒性や可燃性がある危険なガスが使用されるが、それらは大気に放出することができず、無害化するための「除害装置」の設置が必要だ。
危険なガスを無害化する方法として、約1000度以上に加熱して分解する熱酸化反応が主に利用されている。半導体の化学気相合成法※1(CVD)プロセスで多用されるモノシランガスを具体例に説明する。モノシランガスは、爆発下限界※2(LEL)となる1.3パーセント以上の濃度では、空気に触れるだけで爆発的な反応を起こす。そこで、爆発を防ぐためにモノシランガスを窒素ガスによって75倍以上に希釈している。この処理を行う際、希釈によって大量となった排ガスを高温に加熱するため膨大なエネルギーが必要となる。これまで「排ガスを効率良く加熱する手段の開発」や「放熱を抑えて無駄なエネルギーを削減する反応炉の構造開発」は行われていたが、省エネルギーを実現する抜本的な技術開発は進んでいなかった。
※1 化学気相合成法
CVD(Chemical Vapor Deposition)。薄膜材料を製造する合成法の1つで、反応容器内に薄膜の構成元素を含む原料ガスを供給し、基板ウェハー上で原料ガスを分解・化学反応させて基板上に薄膜を堆積させる方法。
※2 爆発下限界
LEL(Lower Explosion Limit)。可燃性ガスまたは可燃性液体の蒸気が空気または酸素と混合した場合、特定のガス濃度範囲で着火源が存在する時に爆発する。この濃度範囲を爆発範囲といい、濃度の低い方の限界を爆発下限界、高い方の限界を爆発上限界という。
ガスを無害化する最適な処理条件を見出す
本開発では、可燃性ガスの爆発下限界が可燃性ガスの圧力に依存することに注目し、希釈ガスの量を削減できる圧力条件を検討した。しかし、可燃性ガスの爆発下限界に関する圧力依存性データは、一般に公開されているものがほとんどなく、水素と空気の反応を高圧側で調べた例がわずかにある程度であった。開発を担当したカンケンテクノでは、さまざまなガスについて独自にデータの取得を積み重ねた。
従来の除外装置(図1)では、デバイス(半導体など)を製造する装置からポンプを使って危険なガスを排出する際、窒素ガスで希釈したうえで、大気圧下で高温加熱処理を行い無害化していた。今回、試作した除害装置(図2)は、製造装置から有毒ガスを排出するポンプ出口から排ガス処理装置内までを真空ポンプによって減圧状態(10キロパスカル程度)にすることにより、配管内のガスの爆発下限界を上げて化学反応を起こさない環境を作り出し、窒素ガスでの希釈を不要にする。また、危険なガスを分解・無害化するために高温加熱する方式を、燃料による燃焼式からプラズマ式に変えた。プラズマ式を実現するため、通常は大気圧(地上では101.3キロパスカル)で発生させるアークプラズマを、0.1~10キロパスカル程度の減圧状態でも安定して発生させられる最適条件を見出した(図3)。これにより、減圧状態の排ガス処理装置内で、アークプラズマ熱源によって危険なガスを酸素と熱反応させ、無害化処理を行うことが可能となった。さらに、実際の排ガス処理で問題となる「無害化処理で発生する副生成物が反応炉内壁に付着すること」を防止するため、反応炉内を水洗浄する仕組みを取り入れた。
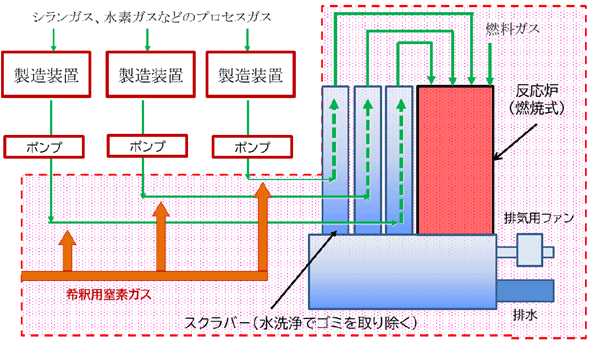
図1 従来の大気圧除害装置の構成例
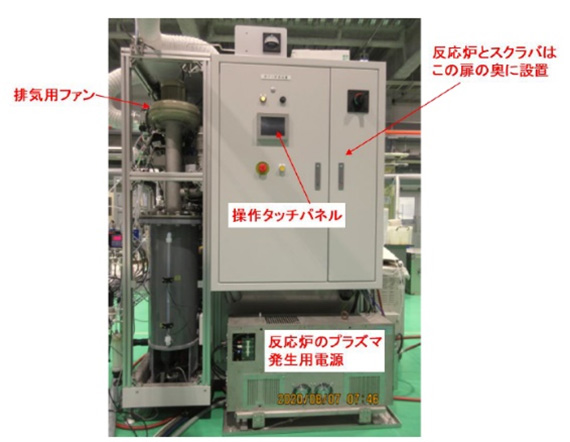
図2 試作した減圧除害装置
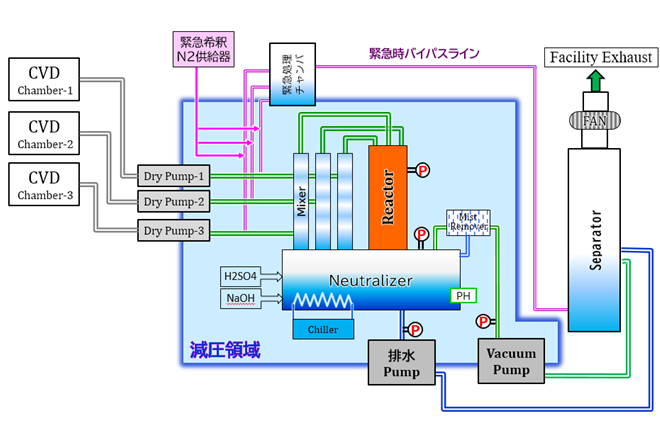
図3 開発した減圧除害装置の構成
水素を使用する幅広い製造装置への応用が進む
新たに開発した除害装置により、エレクトロニクス産業の製造プロセスで大量に使われる窒素ガスを大幅に削減することが可能となる。特に、数多くの工場で稼働しているシランガスを用いたCVDプロセスで窒素ガスによる希釈が不要となる効果は大きい。
加えて省エネルギーのメリットも大いに期待される。窒素ガスによる希釈が行われない分、除害装置に流れ込むガスの総流量は、50分の1~100分の1程度になるため排ガス処理にかかるエネルギー消費を約75パーセント削減できる。昨今、半導体のウェハーサイズもモニターのディスプレイサイズも大きくなり、製造工程ではより多量のシラン系ガスを使用するようになっている。削減できる窒素ガス量が膨大になると、コストおよびエネルギーの削減効果は極めて大きくなる。すでに、排ガス処理の消費エネルギーを大きく削減できる技術として引き合いも多く、半導体製造企業で導入の見込みがある。
さらに、本開発で得た技術は、シランガス以外の窒素ガス希釈を必要とする可燃性ガスにも処理条件を最適化することで、装置の構成を変えずに容易に適用できる。例えば、半導体のシリコンウェハーの水素処理装置やエピタキシャル成長※3装置、有機膜のアッシング※4装置など、水素を使用する製造装置への応用が期待される。
※3 エピタキシャル成長
薄膜結晶成長(単結晶の質量と体積とが同時に増加すること)技術の1つ。 高品位な半導体ウェハーなどに使用される技術。
※4 アッシング
フォトレジスト(半導体の微細加工に用いられる感光性樹脂)などの樹脂表面にラジカルやイオンなどを照射し、樹脂を気化、分解する処理のこと。酸素ガスや水素ガスなどのプラズマが用いられる。
- 環境・エネルギーの成果一覧へ
- 事業成果Topへ
- English