事業成果
車体の軽量化から、低炭素社会の実現まで貢献
金属の強度特性を保つ低温接合を実現2023年度更新
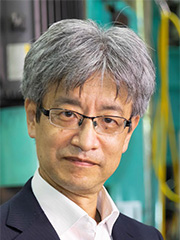
- 藤井 英俊(大阪大学 接合科学研究所 教授)
- 未来社会創造事業
- 「地球規模課題である低炭素社会の実現」領域
「難接合材料を逆活用した接合/分離統合技術の確立」研究開発代表者
(探索研究 2019-2024)
産業界から求められる鋼と鋼の新しい接合方法
鋼板と鋼板の溶接・接合技術は、自動車や鉄道の車両をはじめ、さまざまな工業製品に欠かせない。藤井教授の研究グループは、従来の「抵抗スポット溶接※1」を土台に、「圧力制御通電圧接法※2」として結実した接合技術の要素を組み込み、これまで困難とされていた固相(固体状態のこと)で金属同士の接合を可能にする「固相抵抗スポット接合」を確立した。
従来の「抵抗スポット溶接」は、つなぎたい材料を溶融させるため、炭素量の多い鋼では割れが起こり、接合できなかった。一方、「固相抵抗スポット接合」は、高い圧力をかけながら電流を流すことにより、鋼を溶融させないで、強度特性を変えることのない低温で接合できる。
「固相抵抗スポット接合」で炭素量の多い鋼がうまく接合できるようになると、メーカーにとって材料の選択肢が広がる。また、環境負荷、電力消費、コストの面で圧倒的なメリットがあり、生産効率の向上につながる。さらに接合の過程で出る、溶融された鉄の酸化物(スパッタ)が発生しないため、品質向上に加えて後処理の除去コストの削減にもつながる。
また「固相抵抗スポット接合」のような革新的な接合技術が実用化され、専用の材料やツール・製造装置の開発が進めば、CO2排出量の少ない生産活動、インフラ建設が世界に広がり、低炭素社会の実現にも貢献する(図1)。
※1 抵抗スポット溶接
2枚の金属板を重ねて銅製の電極で加圧しながら大電流を流して、金属に生じる抵抗発熱で溶融部を形成し、板材同士を点で溶接する方法。
※2 圧力制御通電圧接法
接合される材料の端部を突き合わせ、加圧しながら通電することで得られるジュール熱を利用する接合方法。高圧力の付与で、接合温度を材料が変質しない温度に抑えられる。
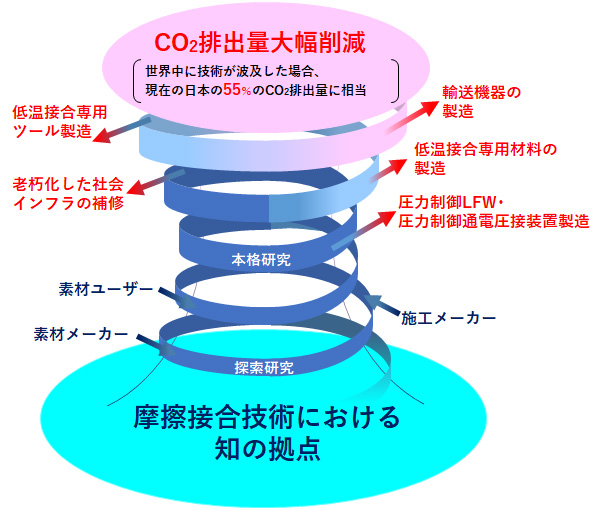
図1 革新的接合技術の実用化による低炭素社会の実現
本来の強度特性を保てなかった従来の接合方法
自動車産業では、車体の軽量化による省エネルギーを目的に、より軽くて丈夫な材料の開発が進められている。車体の多くには、材料として鋼が使われるが、その接合は一筋縄ではいかない技術である。溶接時の発熱などにより相変態し、本来の強度特性を損なうからである。本研究では、鉄道車両や航空機のアルミ合金の接合技術として使われている「摩擦攪拌接合(FSW)」(図2)を発想の原点として研究を重ねて、温度が変化しても材料(鋼)を変態させない新しい接合方法の確立を目指した。
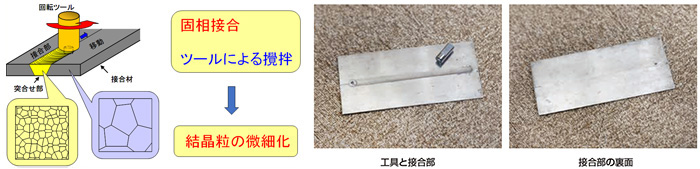
図2 摩擦攪拌接合(FSW:Friction Stir Welding)
先端に突起のある回転ツールを回転させながら強い力で押し付けて突起部を貫入させ、摩擦熱と工具の回転力によって部材を接合する方法。
鋼の強度が低下しない、約700℃での低温接合に成功
工具の回転によって材料の結晶構造をゆがませるとともに、発生する摩擦熱によって再結晶させることで、溶融なしで接合する「摩擦攪拌接合(FSW)」をアルミから鋼に応用するため、研究チームは低い温度での摩擦攪拌接合の可能性を探っていった。鋼は同じ固体の状態でも、結晶の構造が異なる3つの相を持っており、温度変化によって、これらの相が変わる(変態する)と、硬度は高いものの脆い状態になる。より低い温度での摩擦攪拌接合の可能性を探った結果、それまでの摩擦攪拌接合の常識とされていた1000~1200℃よりも低い約700℃での低温接合に成功した。700℃程度であれば、鋼は相変態なしに接合できた。しかし、「摩擦攪拌接合(FSW)」は、攪拌に使用するツールが消耗品であるため、現在の主流となっているアーク溶接※3と比較するとコスト面で課題があった。そこで、さらに効率的な接合技術を求めて、旧来の接合技術「線形摩擦接合(LFW)」(図3)に着目。接合の品質に関わる温度制御の変数となる「金属板を振動させる周波数と振幅」「外側から加える圧力」の関連を解明し、独自の接合技術「圧力制御通電圧接法」を確立して、コンパクトな接合装置を試作した。
※3 アーク溶接
アーク放電という電気的現象を利用して、同じ金属同士をつなぎわせる溶接方法。
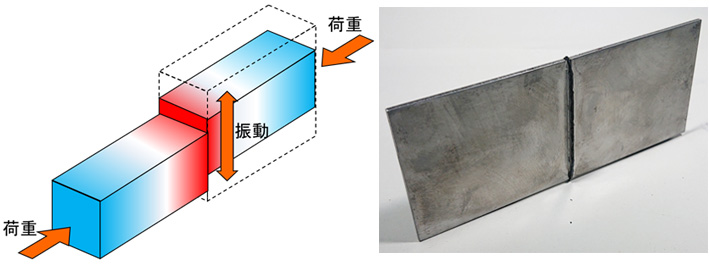
図3 線形摩擦接合(LFW:Linear Friction Welding)
材料同士を押し付けながら片側の部材を線形運動させ、接合面の摩擦熱によって接合させる方法。右の写真は、炭素鋼同士を接合したもの。
「圧力制御通電圧接法」の特長は、2つの材料を接合するため接合面の温度を上げるのに、摩擦熱ではなく電気によるジュール熱を使うことである。2つの金属を突き合わせ、その外側から圧力を加えながら電気を流すと、突き合わせ面はジュール熱で温度が上がり、FSWやLFWと同じ状態を作れる。圧力を上げるほど温度が下がるため、鋼でも相変態なしに接合が可能となる。さらに試作機では、電気を流す電極とは別に加圧用の金属軸を設けることで、これまで追い求めてきた低温接合を実現した。
従来の「抵抗スポット溶接」を土台にしながらも、接合する材料の変態につながる溶融をせず、固相のまま接合するため、新技術は「固相抵抗スポット接合」(図4)と名づけた。
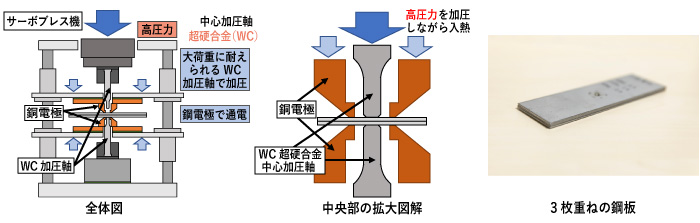
図4 「固相抵抗スポット接合」を取り入れた試作機
「通電用の銅電極」と加圧用のWC(タングステンカーバイド)超硬合金軸による複合構造により、高圧力の印加と通電の両立を実現した。写真は冷間圧延鋼板(SPCC:Steel Plate Cold Commercial)の間に高張力鋼(ハイテン材)を挟んで、3枚の鋼板を接合したもの。
大手メーカーと連携して、自動車産業での実用化を目指す
新たに確立した「固相抵抗スポット接続」の将来性に注目した溶接機・産業用ロボットの大手メーカー株式会社ダイヘンとの産学連携により、試作機(図5)が作られ、実業化へ向けた取り組みが進められている。
製品の品質向上や生産活動における環境負荷の低減を目指す国内外の自動車メーカーからも声が寄せられており、次世代の自動車づくりへの採用が期待される。
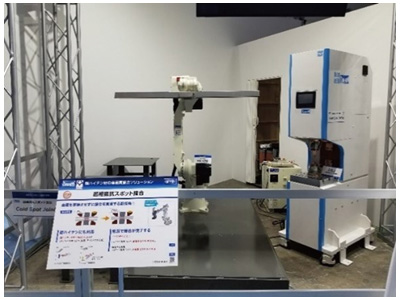
図5 「固相抵抗スポット接合」試作機
- ナノテクノロジー・材料の成果一覧へ
- 事業成果Topへ
- English