事業成果
高機能な高分子多糖類エステル誘導体の創製を実現
天然多糖類からつくるバイオプラスチック2021年度更新
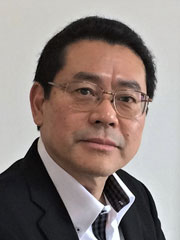
- 岩田 忠久(東京大学 大学院農学生命科学研究科 教授)
- 先端的低炭素化技術開発ALCA
- 特別重点技術領域「ホワイトバイオテクノロジー」
「革新的合成法による高性能な高分子多糖類バイオプラスチックの創製と高機能部材化」研究開発代表者(2015-2019)
革新的な合成法で、新機能を付与
東京大学の岩田忠久教授らは、さまざまな天然、あるいは酵素触媒重合により得られる高分子多糖類から高機能なバイオプラスチックを創製する革新的な合成法を開発した。それにより、従来の石油合成プラスチックにはない、多糖類の特徴的な構造を活かした新しい性能を発現させることに成功した。
これまでプラスチック化できた天然、あるいは酵素触媒重合によって得られた高分子多糖類としては、木材由来の高分子多糖類であるセルロース、ミドリムシが合成するパラミロン、針葉樹やこんにゃく芋に含まれるグルコマンナン、微生物が発酵により生成するカードランやプルランなどがある。
これらを原料としたバイオプラスチックに、目的に応じた強度、耐熱性、光特性、寸法安定性、耐久性などの性能をもたせることに成功した。実用化に向けた成果の一例としては、漆黒の美しさと高度な耐傷性を備えた高級漆器調のバイオプラスチック「漆ブラック」がある。
また、環境や人体に有害な物質を使わずにプラスチックを生成する研究や、オーバースペックではない、適材適所に使用できる高分子多糖類バイオプラスチックライブラリーの構築も進め、石油からバイオマスへの原料転換への道をつけつつある。
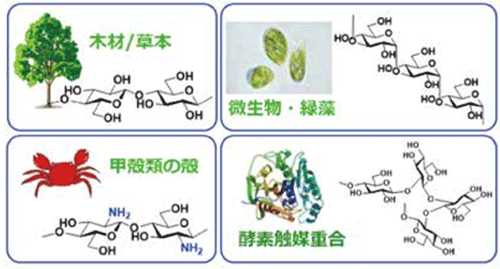
図1 天然の高分子多糖類と酵素触媒重合
脱石油で環境問題に配慮
石油を原料としてつくるプラスチックは社会の多様な場面で使用されているが、近年、地球温暖化を促進する二酸化炭素排出や石油資源の枯渇、廃棄プラスチックによる環境汚染など、さまざまな問題から石油原料に代わる再生可能原料の開発が急がれている。そこで注目されているのが、植物成分を原料とするバイオプラスチックや、環境中で分解する生分解性プラスチックなどの環境負荷の低いプラスチックである。
また、石油からプラスチックを合成する過程では、通常、金属触媒が用いられ、バイオプラスチックの原料を植物から抽出するときには有機溶剤が用いられるが、金属触媒や有機溶剤など、環境や人体に有害な物質を用いずにプラスチックを合成する方法も模索されてきた。
本研究はそういった社会情勢を踏まえて進められているものだ。特に、単なる石油合成プラスチックの代替物ではない、バイオマス由来ならではの物性や機能をもつ高付加価値なバイオプラスチックをつくることを目指している。
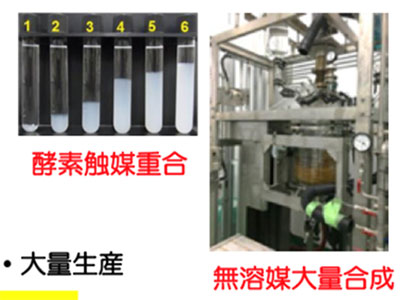
図2 酵素触媒重合と無溶媒大量合成のプロセス
意匠性・耐傷性の高さも実現
多糖類にはバイオプラスチック原料として高いポテンシャルがあるが、抽出が困難、純度が低いなどの理由で、これまで活用されてこなかった。本研究では多糖類から耐熱性、耐衝撃性、光学特性に優れたさまざまな長鎖・短鎖多糖類エステル誘導体を合成することに成功し、自然由来の材料ならではの構造を生かした、新規で高性能なバイオプラスチックを創製した。
また、一般に多糖類バイオプラスチックを成型加工する際には、流動性や物性の制御のために石油由来の可塑剤を添加し、誘導体化の工程においては有機溶媒を使用する。それに対して本プロジェクトでは、添加剤を用いなくても成形加工できるバイオプラスチック製品の開発や、有機溶媒の使用量を減らす工程の開発を行った。さらに、低エネルギー大量合成法も確立した。
バイオプラスチックがさまざまな場面で使用されるようになるには、高機能であることも重要である。本研究では、樹脂改質や複合化による、付加価値の高い環境調和型の高機能部材としての開発を進め、高級漆器のような漆黒の美しさを持つ「漆ブラック調バイオプラスチック」を開発した。これはセルロース系のバイオプラスチックで、意匠性の高い外観を保持するため、セルロース系に有効な添加成分の配合技術を新たに開発し、低い明度、高い光沢度、漆特有の深さと温かさといった光学特性と、高度な耐傷性の両立を実現することに成功した。
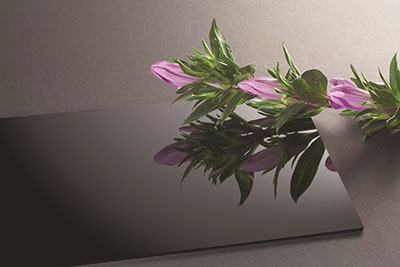
図3 漆器の美しさを実現したセルロース系のバイオプラスチック
環境配慮、高機能化、低コスト化を目指す
「漆ブラック」のほか、フィルムや繊維、成形品なども、すでにこれらの手法により開発されているが、今後もさまざまな多糖類から、熱成形加工が可能で機能性や装飾性に優れた部材の開発を続けていく。
また、酵素触媒合成や無溶媒反応など、有機溶媒や金属触媒に依存しない合成法の研究開発を継続し、さらに低エネルギーで環境負荷の低い環境調和型バイオプラスチックを生み出していく。
将来的には、実用化を推進するために石油由来のプラスチックと同等のコストとなることを目指し、低コスト化を実現する合成プロセスの開発にも取り組む予定である。
- 環境エネルギーの成果一覧へ
- 事業成果Topへ
- English