事業成果
低炭素社会の切り札
強くて軽く安価な「マグネシウム合金」2020年度更新
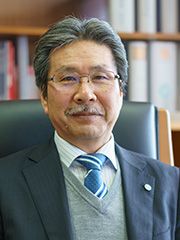
- 鎌土 重晴(長岡技術科学大学 理事・副学長/技学研究院 教授)
- ALCA
- 実用技術化プロジェクト「省エネルギー社会に向けた革新的軽量材料の創製」
「軽量構造部材創製のための革新的汎用マグネシウム合金の開発」研究開発代表者(2012-2019)
アルミニウム合金に代わる次世代「マグネシウム合金」
現在、強度と軽さを兼ね備えた「アルミニウム合金」が新幹線をはじめとした鉄道のほか、自動車や航空機などの輸送機器の構造材料として多用されている。しかし、さらなる軽量化が実現すれば、輸送機器の燃費が向上し、二酸化炭素(CO2)の排出量を大幅に削減できる。そこで、期待されているのが、アルミニウム合金の比重の3分の2と、実用金属の中で最も軽い「マグネシウム合金」の実用化だ。実際、パソコンやカメラのフレームなどへの利用は拡大しているものの、室温での強度や加工性の面で課題があり、輸送機器への応用は進んでいない。
それに対し、ALCAの研究開発代表者の鎌土重晴教授は、既存の鉄鋼材料やアルミニウム合金に匹敵し、室温での強度と加工性を併せ持つ画期的なマグネシウム合金の開発に成功した。その強度は、現在、新幹線の車体に利用されているアルミニウム合金をも上回る。
実用化に向けた最終目標は、幅広い輸送機器への応用だが、その第一歩として、自動車部材への適用を目指して開発を進めている。
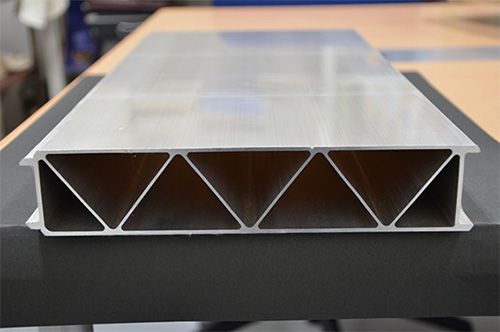
図1 新規開発のマグネシウム合金。高速押出成形にて試作した新幹線モデル構体
「G.P.ゾーン」により強度と加工性を両立
従来のマグネシウム合金は、主にダイカストと呼ばれる金型鋳造法で作られている。これは高温で溶かした合金を金型に入れ冷やし固めるというものだ。しかし、これでは十分な強度は得られない。
強度を高める加工方法としては、押出成形と圧延の2通りがある。ところが、既存のマグネシウム合金には加工がしにくいという欠点がある。押出成形の場合、マグネシウム合金の押出速度は、建築用のサッシや自動車のボディに使われている「6000系」と呼ばれる中強度アルミニウム合金の半分以下しかない。そのため、大量生産ができない。
それに対し、鎌土教授は従来のマグネシウム合金に、微量のアルミニウム、マンガンのほか、新たにカルシウムを加えたことで、6000系アルミニウム合金に匹敵する強度と加工性の両立を実現した。その鍵は、1原子層厚さの薄い板状の原子集合体「G.P. (Guinier-Preston) ゾーン」である。添加したアルミニウムやカルシウムを高温で溶解すると合金の塊ができる。これを押出成形した後、約200℃の環境の中に一定時間入れると、G.P.ゾーンが合金の中に形成され、強度が大幅に増す。このような金属や合金のある性質が時間の経過とともに変化する現象を「時効」という。
鎌土教授は、2013年には、1分間に60メートルの速度での押出成形を成功させた。さらに、このマグネシウム合金に約200℃で15~30分程度の短時間の時効処理を施すだけで、G.P.ゾーンが析出し、新幹線の車体に使われているアルミニウム合金を上回る強度になることがわかった。
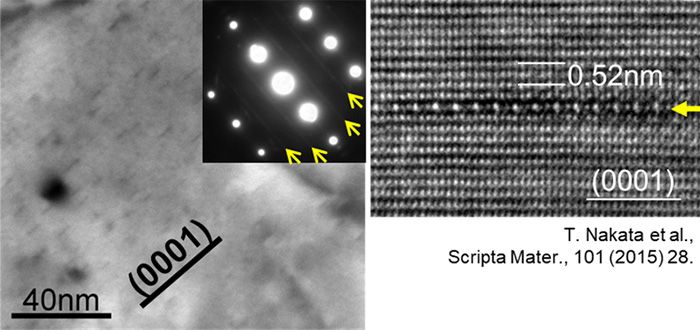
図2 原子層レベルの薄い板状の原子集合体「G.P.ゾーン」の析出により、新幹線の車体に使われているアルミニウム合金を上回る強度に
コンピューター・シミュレーションを駆使することで合金の組成をナノ・ミクロレベルで予測
鎌土教授は圧延板材の開発も進めた。コストの面から、室温で加工できること、添加する元素はレアアースのような高価な元素ではなくありふれた元素を使うことを必須条件とした。そして、押出成形に成功したマグネシウム合金に、さらに微量の亜鉛を添加した結果、結晶配向が制御され、アルミニウム合金並みに丸く室温成形できることを示した。これは、微量の亜鉛添加により、「六方最密充填構造」と呼ばれる六角柱の配向が変化し、加工性が高まったためである。さらに、自動車のボディパネル材に施される熱履歴に相当する170℃で20分間という短時間の時効処理を施すことで、強度が飛躍的に向上することも世界で初めて明らかにした。
このように、マグネシウム合金の特性は加える元素の配合比率を少し変えるだけで大きく変化する。そのため、鎌土教授はさまざまな種類のコンピューター・シミュレーションを駆使することで、G.P.ゾーンを形成する合金系を探索する指針の導出、そして、形成されたG.P.ゾーンの成長を再現した。その結果、ナノ・ミクロ組織の組成の予測が可能となり、今回の成果につながったのである。また、シミュレーション結果は、実験結果とも合致したことから、形成されたG.P.ゾーンの検証が可能となった。加えて、添加した元素が強度の向上に寄与するメカニズムも原子レベルで明らかになってきた。
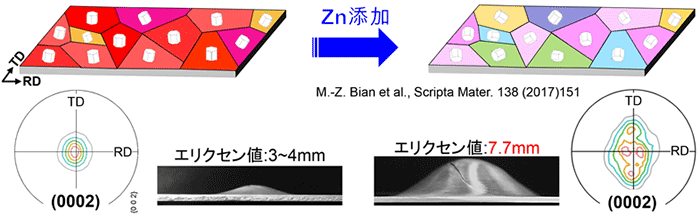
図3 押出成形に成功したマグネシウム合金に、さらに微量の亜鉛を添加した結果、アルミニウム合金並みに丸く室温成形できることを示した
最終目標は自動車や鉄道への応用
今後、鎌土教授はこれらの成果を基に、新たにどのような元素をどれくらい添加すれば欲しい性能を出すことができるかを探っていく。また、押出成形や圧延により形成される合金の組織構造をコンピューター・シミュレーションで詳細に調べていくことで、どのような温度領域で加工すべきか、どのような熱処理や時効処理を施せばよいかなどを明らかにし、体系化していく。それにより、製造プロセスの最適化を図っていく。そして、最終目標である自動車や鉄道など幅広い輸送機器への応用を目指す。
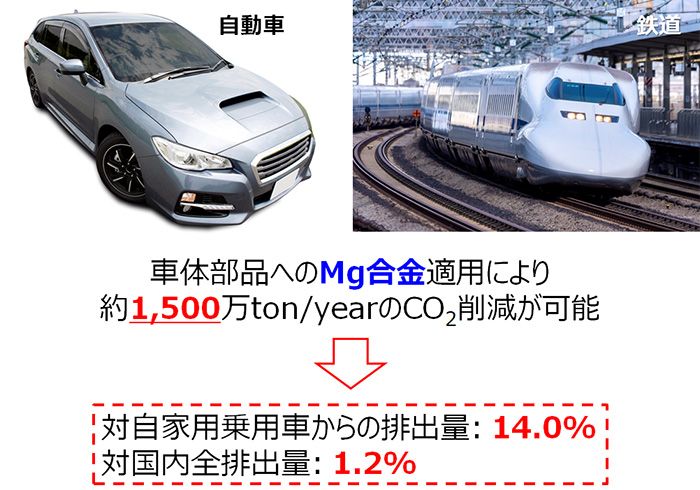
図4 最終目標は自動車や鉄道など幅広い輸送機器への応用。それにより、CO2排出量を大幅に削減できる
- ナノテクノロジー・材料の成果一覧へ
- 事業成果Topへ
- English